ZnO nanosheet grown carbon fiber cloth reinforced polyhexahydrotriazine composite material, preparation method and recovery method
A technology of polyhexahydrotriazine and carbon fiber cloth, which is applied in the fields of carbon fiber, plastic recycling, fiber processing, etc., can solve the problems of unrealistic industrial production, poor wear resistance, complicated preparation process, etc., and achieve simple and easy parameter adjustment , The preparation method is simple and easy, and the effect of expanding the application range and prospect
- Summary
- Abstract
- Description
- Claims
- Application Information
AI Technical Summary
Problems solved by technology
Method used
Image
Examples
preparation example Construction
[0026] The invention provides a method for preparing a polyhexahydrotriazine composite material reinforced by growing ZnO nanosheet carbon fiber cloth, comprising the following steps:
[0027] Step 1: Electroplating the carbon fiber cloth, covering the surface of the carbon fiber cloth with zinc to obtain Zn@CFC; the preparation of the electroplating solution is ZnCl 2 , KCl, H 3 BO 3 and C 7 h 5 NO 3 Add S into deionized water, use a magnetic stirrer to stir at room temperature for 25 to 40 minutes, fully stir and disperse evenly, and ZnCl in the electroplating solution 2 The concentration of KCl is 50-70g / L, the concentration of KCl is 180-240g / L, the concentration of H 3 BO 3 The concentration is 15~20ml / L, C 7 h 5 NO 3 The concentration of S is 0.3 ~ 0.5g / L; the carbon fiber cloth is pretreated before electroplating treatment. The pretreatment is: put the commercial carbon fiber weave into the mixed solution of absolute ethanol and acetone for ultrasonic cleaning,...
Embodiment 1
[0037] 1) Coating zinc on the surface of CF by electroplating process at room temperature: electroplating time is 5min, current intensity is 4.5A, voltage is 4.0V, Zn@CFC material is obtained, and cleaned with distilled water;
[0038] 2) Covering ZnO nanosheets on the CF surface by oxidation: ZnO@CFC material was synthesized by oxidizing Zn@CFC material at 80°C for 3 hours and cooling to room temperature naturally;
[0039] 3) Preparation of PHT prepolymer solution: 600 μL of formaldehyde, 15 mL of N-methylpyrrolidone and 2 g of 4,4’-diaminodiphenyl ether were stirred at 50 ° C for 30 minutes;
[0040] 4) Cover PHT on ZnO@CFC by solution impregnation method: dry the ZnO@CFC soaked in PHT for 5-10 minutes, repeat at least 5 times until the thickness of the sample reaches 0.35-0.55mm, and then, the obtained pre- The polymer composite material is further cured at 180-200° C. for 2 hours to obtain a two-dimensional ZnO nanosheet and CF-reinforced polyhexahydrotriazine composite m...
Embodiment 2
[0043] Using the same method as in Example 1, the difference is that the prepared PHT prepolymer solution uses 650 μL of formaldehyde, 16 mL of N-methylpyrrolidone and 3 g of 4,4'-diaminodiphenyl ether at 50 ° C Stir the resultant for 30 minutes.
PUM
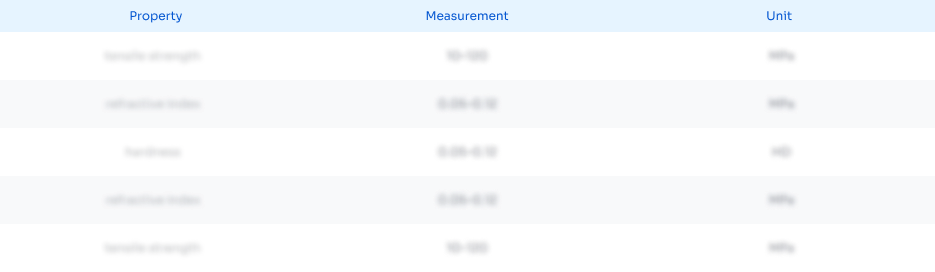
Abstract
Description
Claims
Application Information

- Generate Ideas
- Intellectual Property
- Life Sciences
- Materials
- Tech Scout
- Unparalleled Data Quality
- Higher Quality Content
- 60% Fewer Hallucinations
Browse by: Latest US Patents, China's latest patents, Technical Efficacy Thesaurus, Application Domain, Technology Topic, Popular Technical Reports.
© 2025 PatSnap. All rights reserved.Legal|Privacy policy|Modern Slavery Act Transparency Statement|Sitemap|About US| Contact US: help@patsnap.com