Bio-based flame-retardant magnolol epoxy monomer, preparation method thereof and application of monomer in flame-retardant epoxy resin
An epoxy resin, bio-based technology, applied in the field of polymer chemistry, can solve the problem of relatively little research on flame retardant properties, and achieve the effects of simple and efficient curing process, low usage, and high biological safety.
- Summary
- Abstract
- Description
- Claims
- Application Information
AI Technical Summary
Problems solved by technology
Method used
Image
Examples
Embodiment 1
[0077] Embodiment 1: Preparation of bio-based flame retardant magnolol epoxy monomer:
[0078] First, add magnolol (9.98g, 37.5mmol) and sodium hydride (1.98g, 82.5mmol) successively in a clean three-necked flask, and add excess tetrahydrofuran (200mL) under ice bath to fully dissolve it, and the reaction system Filled with nitrogen and kept stirring under ice bath conditions for 15min, slowly added diphenylphosphinoyl chloride (19.52g, 82.5mmol) with a 50mL syringe, stirred at room temperature for 3h, when the reaction was complete, mixed ethyl acetate and deionized water Add the solution with a volume ratio of 1:1 (each 60 mL) into the reaction solution cooled in an ice bath, let it stand for 30 minutes, add a small amount of saturated saline, extract the reaction solution with ethyl acetate, combine the organic phases, and dry over anhydrous sodium sulfate The organic phase was filtered and distilled under reduced pressure to obtain the crude product of intermediate DBDBD; ...
Embodiment 2
[0081] Take by weighing DGEBA monomer (0.1g, 0.29mmol) in the sample bottle, epoxy resin monomer BOBDB (0.037g, 0.053mmol), promptly the P element content accounts for 2wt% of reaction system gross mass in the epoxy resin monomer BOBDB, Introduce nitrogen to remove oxygen components, add menthanediamine (0.025g, 0.145mmol) under nitrogen atmosphere, further remove air, heat up to 55°C to melt the two (melting process is transparent and uniform) and mix well , Cured at 200°C for 3h to obtain light yellow transparent epoxy resin polymer. Micro-combustion calorimetry (MCC) experiment results show that the maximum heat release rate is 431.95W / g.
Embodiment 3
[0083] Take by weighing DGEBA monomer (0.1g, 0.29mmol) in the sample bottle, epoxy resin monomer BOBDB (0.11g, 0.016mmol), promptly the P element content accounts for 4wt% of reaction system gross mass in the epoxy resin monomer BOBDB, Introduce nitrogen to remove oxygen components, add menthanediamine (0.025g, 0.145mmol) under nitrogen atmosphere, further remove air, heat up to 65°C to melt the two (melting process is transparent and uniform) and mix well , 200 ° C curing, curing 3h, to obtain light yellow transparent epoxy resin polymer. Micro-combustion calorimetry (MCC) experiment results show that the maximum heat release rate is 303.24W / g.
PUM
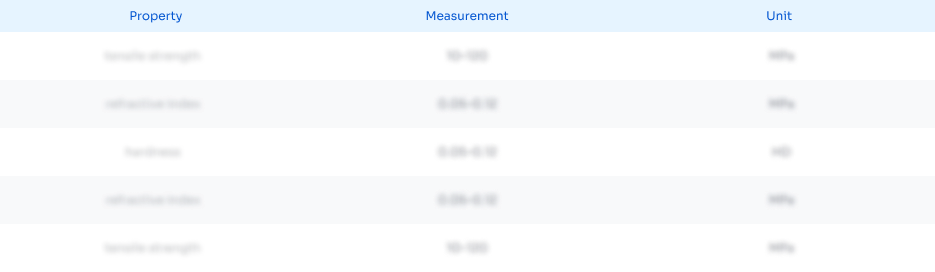
Abstract
Description
Claims
Application Information

- R&D Engineer
- R&D Manager
- IP Professional
- Industry Leading Data Capabilities
- Powerful AI technology
- Patent DNA Extraction
Browse by: Latest US Patents, China's latest patents, Technical Efficacy Thesaurus, Application Domain, Technology Topic, Popular Technical Reports.
© 2024 PatSnap. All rights reserved.Legal|Privacy policy|Modern Slavery Act Transparency Statement|Sitemap|About US| Contact US: help@patsnap.com