a blown co 2 Dynamic control method of stainless steel smelting process
A dynamic control, CO2 technology, applied in non-electric variable control, temperature control using electric mode, temperature control and other directions, can solve the problems of low decarburization rate of molten pool, insufficient stirring intensity, melting loss of furnace lining refractory, etc. Improve the smelting efficiency, improve the stirring performance of the molten pool, and reduce the effect of high temperature melting loss
- Summary
- Abstract
- Description
- Claims
- Application Information
AI Technical Summary
Problems solved by technology
Method used
Image
Examples
Embodiment 1
[0037] The invention is applied to the refining process of a 180t AOD furnace, and the smelted product is 304 stainless steel. The smelting raw materials are stainless steel mother liquor and high-carbon ferrochrome, and the smelting time is set for the rapid decarburization period t 1 15min, the temperature control period set the smelting time t 2 8min, set the smelting time t in the deep decarburization period 3 for 15min, the proportionality factor R 1-CO2 Take the value of 0.1, R 3-CO2 Take the value of 0.05, R 3-N2 / Ar The value is 2. The specific smelting steps are as follows:
[0038] (1) The components of stainless steel mother liquor and high-carbon ferrochrome are obtained from the raw material acquisition system in the steelmaking control system, as shown in Table 1 and Table 2. The weight of the stainless steel mother liquor is 175t, and the preset target composition is shown in Table 3. The amount of steel is 180t.
[0039] Table 1 stainless steel mother liq...
Embodiment 2
[0050] The invention is applied to the 70t TSR stainless steel smelting process, and the smelted product is 410 stainless steel. The smelting raw materials are dephosphorized hot metal and high-carbon ferrochromium, and the smelting time is set for the rapid decarburization period t 1 20min, the temperature control period is set to smelting time t 2 10min, the deep decarburization period sets the smelting time t 3 is 22min, the proportionality factor R 1-CO2 Take the value of 0.1, R 3-CO2 Take the value of 0.06, R 3-N2 / Ar The value is 2. The specific smelting steps are as follows:
[0051] (1) The composition of dephosphorized hot metal and high-carbon ferrochrome obtained from the raw material acquisition system in the steelmaking control system is shown in Table 1 and Table 2. The weight of the stainless steel mother liquor is 66t, and the preset target composition is shown in Table 3. The target The tapping amount is 70t.
[0052] Table 1 Composition of dephosphorize...
PUM
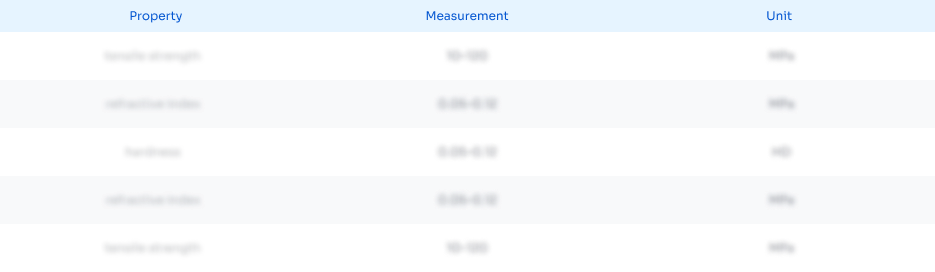
Abstract
Description
Claims
Application Information

- R&D
- Intellectual Property
- Life Sciences
- Materials
- Tech Scout
- Unparalleled Data Quality
- Higher Quality Content
- 60% Fewer Hallucinations
Browse by: Latest US Patents, China's latest patents, Technical Efficacy Thesaurus, Application Domain, Technology Topic, Popular Technical Reports.
© 2025 PatSnap. All rights reserved.Legal|Privacy policy|Modern Slavery Act Transparency Statement|Sitemap|About US| Contact US: help@patsnap.com