Polyethylene fiber composite cloth with high protection performance and preparation and application thereof
A technology of polyethylene fiber and composite cloth, applied in protective equipment, protective equipment, applications, etc., can solve the problems of increasing the bulletproof discreteness of polyethylene fiber composite cloth and affecting the appearance quality of products, and achieve the improvement of the interlayer adhesion of composite cloth. Bonding and anti-ballistic properties, reducing hair and broken wires, and reducing artificial effects
- Summary
- Abstract
- Description
- Claims
- Application Information
AI Technical Summary
Problems solved by technology
Method used
Image
Examples
Embodiment 1
[0036]UHMWPE fibers with bundle fineness of 1500D, single filament fineness of 3.1D, tensile strength of 34cN / dtex, and tensile modulus of 1100cN / dtex are used to prepare polyethylene fiber composite cloth, and the fibers are unwound from the creel and laid flat , after heating and drawing, gluing, drying, and winding to obtain unidirectional polyethylene fiber cloth. Among them, the temperature of heating and drawing is 155°C, the drawing ratio is 2.5 times, the fineness of polyethylene bundle after drawing is about 600D, the fineness of single filament is about 1.25D, the tensile strength is about 37.5cN / dtex, and the tensile modulus is about 1380cN / dtex; gluing adopts the method of fiber dipping in water-based polyurethane glue tank, in which the activation temperature of polyurethane is 110°C, and the oven drying adopts the method of 3-stage temperature gradient reduction, and the three-stage temperatures are 100°C and 90°C respectively , 80°C; after winding, the surface d...
Embodiment 2
[0039] UHMWPE fibers with bundle fineness of 800D, single filament fineness of 2D, tensile strength of 36cN / dtex, and tensile modulus of 1250cN / dtex are used to prepare polyethylene fiber composite cloth, and the fibers are unwound from the creel and laid flat. After heating and drawing, gluing, laminating, drying and winding, the unidirectional polyethylene fiber cloth is obtained. Among them, the temperature of heating and drawing is 160°C, the drawing ratio is 2 times, the fineness of the polyethylene fiber bundle after drawing is about 400D, the single filament fineness is about 1D, the tensile strength is about 40.2cN / dtex, and the tensile modulus is about 1500cN / dtex; gluing adopts the method of fiber dipping in water-based polyacrylic glue tank, in which the activation temperature of polyacrylic glue is 95°C, and the oven drying adopts the method of 4-stage temperature gradient reduction, and the temperature of the four stages is 90°C respectively , 85°C, 80°C, 75°C; ot...
Embodiment 3
[0051] A preparation method of polyethylene fiber composite cloth with high protection performance, comprising the following steps:
[0052] 1) The ultra-high molecular weight polyethylene fiber with high denier is unwinded and laid, heated and drawn, glued and dried in sequence to obtain a unidirectional polyethylene fiber cloth;
[0053] 2) After the multi-layer unidirectional polyethylene fiber cloth is cross-laminated and compounded, it is rolled together with the isolation layer, and then vacuum hot-pressed to obtain a polyethylene fiber composite cloth. In the polyethylene fiber composite cloth, the glue content is 5wt%.
[0054] In step 1), the activation temperature of the glue is 150°C. The monofilament fineness of ultra-high molecular weight polyethylene fiber is ≥2D, the bundle fineness is ≥800D, the tensile strength is ≥32cN / dtex, and the tensile modulus is ≥800cN / dtex. During the heating and drawing process, the heating temperature is 120° C., and the drawing ra...
PUM
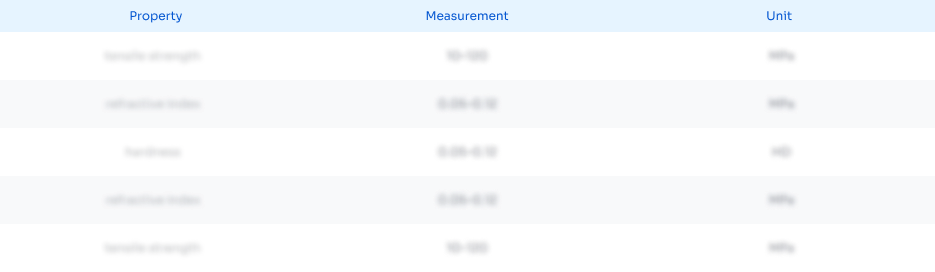
Abstract
Description
Claims
Application Information

- R&D
- Intellectual Property
- Life Sciences
- Materials
- Tech Scout
- Unparalleled Data Quality
- Higher Quality Content
- 60% Fewer Hallucinations
Browse by: Latest US Patents, China's latest patents, Technical Efficacy Thesaurus, Application Domain, Technology Topic, Popular Technical Reports.
© 2025 PatSnap. All rights reserved.Legal|Privacy policy|Modern Slavery Act Transparency Statement|Sitemap|About US| Contact US: help@patsnap.com