Method of jointing target material and back plate
A bonding method and backplane technology, applied in welding equipment, non-electric welding equipment, metal processing equipment, etc., can solve the problems of easy generation of defects, unstable accumulated use time, and decreased adhesion rate, and achieve the effect of reducing bonding defects.
- Summary
- Abstract
- Description
- Claims
- Application Information
AI Technical Summary
Problems solved by technology
Method used
Image
Examples
Embodiment 1
[0015] A bonding method for a target and a backplate, such as figure 1 The following steps are shown:
[0016] (1) Preheat the metal sheath 2 with the built-in heater 1 to 350°C as a whole, and then place it on the machine tool 6 of the hydraulic press;
[0017] (2) Just insert the back plate 3 into the groove of the metal sheath 2, place the target material 4 in the center of the upper surface of the back plate, and then place a briquetting block 5 having the same diameter as the back plate 3 on the upper surface of the target material 4;
[0018] (3) Heat the back plate 3 and the target material 4 to 400°C, and apply 8kg / mm to the upper surface of the compact 5 2 After maintaining the temperature and pressure for 45 minutes, take out the back plate 3 and the target material 4, that is, complete the bonding of the back plate 3 and the target material 4, and check the defects of the bonding layer by an ultrasonic flaw detection machine, and more than 99% of the defects can ...
Embodiment 2
[0021] With above-mentioned embodiment 1, its difference is:
[0022] (1) Preheat the metal sheath 2 of the built-in heater 1 to 300°C as a whole, and then place it on the machine tool 6 of the hydraulic press;
[0023] (2) Just insert the back plate 3 into the groove of the metal sheath 2, place the target material 4 in the center of the upper surface of the back plate, and then place a briquetting block 5 having the same diameter as the back plate 3 on the upper surface of the target material 4;
[0024] (3) Heat the back plate 3 and the target 4 to 300°C, and apply 3kg / mm to the upper surface of the compact 5 2 After keeping at this temperature and pressure for 120 minutes, take out the back plate 3 and the target material 4, that is, complete the bonding of the back plate 3 and the target material 4, and check the defects of the bonding layer by an ultrasonic flaw detection machine, and more than 99% of the defects can be obtained. the attachment rate.
Embodiment 3
[0026] With above-mentioned embodiment 1, its difference is:
[0027] (1) Preheat the metal sheath 2 of the built-in heater 1 to 400°C as a whole, and then place it on the machine tool 6 of the hydraulic press;
[0028] (2) Just insert the back plate 3 into the groove of the metal sheath 2, place the target material 4 in the center of the upper surface of the back plate, and then place a briquetting block 5 having the same diameter as the back plate 3 on the upper surface of the target material 4;
[0029] (3) Heat the back plate 3 and the target material 4 to 600°C, and apply 10kg / mm to the upper surface of the compact 5 2 After maintaining the temperature and pressure for 30 minutes, take out the back plate 3 and the target material 4, that is, complete the bonding of the back plate 3 and the target material 4, and check the defects of the bonding layer by an ultrasonic flaw detection machine, and more than 99% of the defects can be obtained. the attachment rate.
PUM
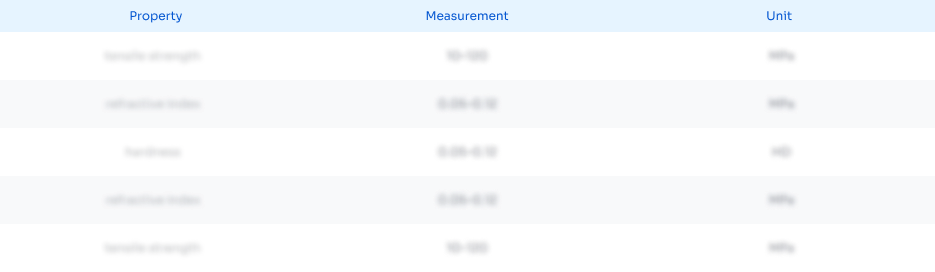
Abstract
Description
Claims
Application Information

- R&D
- Intellectual Property
- Life Sciences
- Materials
- Tech Scout
- Unparalleled Data Quality
- Higher Quality Content
- 60% Fewer Hallucinations
Browse by: Latest US Patents, China's latest patents, Technical Efficacy Thesaurus, Application Domain, Technology Topic, Popular Technical Reports.
© 2025 PatSnap. All rights reserved.Legal|Privacy policy|Modern Slavery Act Transparency Statement|Sitemap|About US| Contact US: help@patsnap.com