A Cylindrical Grinding Device for Hydraulic Compensation Valve Core
A technology of processing device and compensation valve, which is applied in metal processing equipment, grinding workpiece supports, manufacturing tools, etc., can solve the problem of small external tolerance of hydraulic compensation valve core, placement of hydraulic compensation valve core, and reduce the safety of cylindrical grinding processing device. problems such as performance and effect, to improve processing efficiency and avoid wear and tear
- Summary
- Abstract
- Description
- Claims
- Application Information
AI Technical Summary
Problems solved by technology
Method used
Image
Examples
Embodiment 1
[0033] Example 1, such as figure 1 , 2 , 3, 4, 5 and 7, when replacing a new hydraulic compensating spool 410, when the hydraulic compensating spool 410 at both ends of a set of grinding jacket 405 has been ground, the first servo motor 406 drives the guide The roller 403 rotates 180° clockwise, so that the next set of fixed grinding jacket 405 and hydraulic compensation valve core 410 rotate to the position close to the grinding wheel 11, and the two sets of hydraulic compensation valve cores 410 that have been ground Then turn to the end away from the grinding wheel 11, the operator manually turns the threaded hole 409 on the set of grinding jacket 405 to face the electric screwdriver 5, and then loosens the screw 408 through the electric screwdriver 5, and then controls the second servo motor 701 to reverse Rotate to make the two groups of horizontal plates 704 away from each other, which also makes the splint 707 away from each other, so that the hydraulic compensation va...
Embodiment 2
[0034] Example 2, such as Figure 1-7 As shown, when processing the hydraulic compensation spool 410, the third servo motor 709 is controlled to rotate in the same direction as the grinding wheel 11, and the third servo motor 709 drives the connected splint 707 to drive the connected two sets of hydraulic compensation spools 410 and The grinding jacket 405 rotates in the same direction synchronously, and then the electric push rod 15 is controlled to push the installation chamber 2 to move, so that the surface of the grinding wheel 11 is in contact with the surface of the hydraulic compensation spool 410 , and the surface of the hydraulic compensation spool 410 is ground.
[0035] Working principle: connect the device to the power supply before use, first place the same ends of the two sets of hydraulic compensating spools 410 on the two sets of rollers on the top of a set of arc-shaped plates 402, and then control the second servo motor 701 through the control panel 6 Forward...
PUM
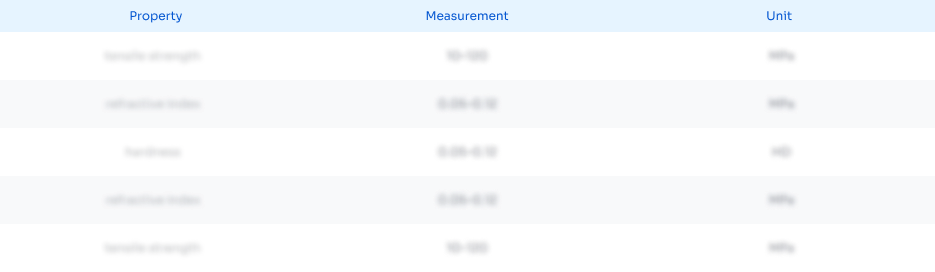
Abstract
Description
Claims
Application Information

- R&D Engineer
- R&D Manager
- IP Professional
- Industry Leading Data Capabilities
- Powerful AI technology
- Patent DNA Extraction
Browse by: Latest US Patents, China's latest patents, Technical Efficacy Thesaurus, Application Domain, Technology Topic, Popular Technical Reports.
© 2024 PatSnap. All rights reserved.Legal|Privacy policy|Modern Slavery Act Transparency Statement|Sitemap|About US| Contact US: help@patsnap.com