Path planning and swing reduction control method of a four-rotor variable-rope length suspension system
A technology of path planning and control method, applied in the field of quadrotor control, can solve the problems of accuracy dependence of model establishment, low interference robustness, long time, etc., to improve transportation efficiency, ensure safety, and suppress swing. Effect
- Summary
- Abstract
- Description
- Claims
- Application Information
AI Technical Summary
Problems solved by technology
Method used
Image
Examples
Embodiment 1
[0208] Setting parameters: quadrotor mass M=1.4kg, load mass m=0.25kg, gravitational acceleration g=9.81m / s 2 , the moment of inertia J x =0.0087kg m 2 , J y =0.0087kg m 2 , J z =0.016kg m 2 , J r =9.89e-5kg m 2, the length of the sling changes with time as L=1+0.1t m, the distance between the motor and the center of the quadrotor is d=0.18m, and the initial position of the quadrotor is [x r0 ,y r0 ,z r0 ]=[0,0,0], the desired position is [x r ,y r ,z r ]=[3,4,5], the upper and lower limits of the transportation time T are respectively T l =4s, T u =7s, limit the maximum swing angle to α max =β max =0.3rad, the maximum swing rate is The T value calculated by dichotomy was 5.0313.
[0209] The quadrotor reference trajectory calculated according to the above method is:
[0210]
[0211]
[0212] Simulation experiment: use matlab for simulation analysis, see the simulation results Figure 5-Figure 12 . The results show that the quadrotor can carry the l...
PUM
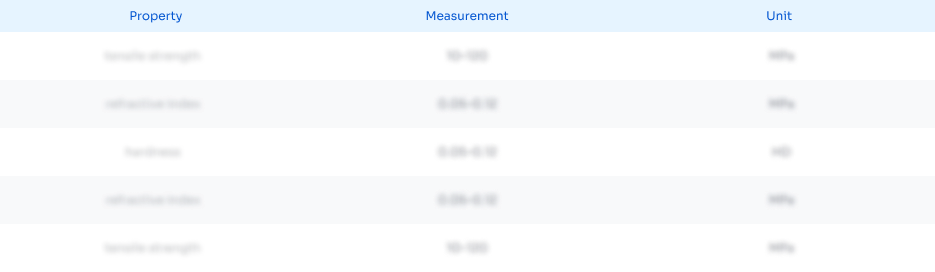
Abstract
Description
Claims
Application Information

- R&D Engineer
- R&D Manager
- IP Professional
- Industry Leading Data Capabilities
- Powerful AI technology
- Patent DNA Extraction
Browse by: Latest US Patents, China's latest patents, Technical Efficacy Thesaurus, Application Domain, Technology Topic, Popular Technical Reports.
© 2024 PatSnap. All rights reserved.Legal|Privacy policy|Modern Slavery Act Transparency Statement|Sitemap|About US| Contact US: help@patsnap.com