Control method for implementing coordinated operation of multiple vehicle groups of hydraulic heavy duty truck
A control method and technology for trucks, applied in the field of measurement and control, can solve problems such as difficult production safety, high personnel requirements, and driver influence, and achieve the effects of ensuring stability and accuracy, expanding the scope of work, and avoiding potential safety hazards.
- Summary
- Abstract
- Description
- Claims
- Application Information
AI Technical Summary
Problems solved by technology
Method used
Image
Examples
Embodiment Construction
[0029] 1. Ultrasonic ranging system
[0030] Such as figure 1 As shown, the ultrasonic ranging sensor is composed of 1 transmitter and 2 receivers. Transmitter 1 emits ultrasonic transmission line 4. When the ultrasonic ray touches the roadway wall 3, it will bounce back, and receiver 2 is used to receive the bounced ultrasonic waves. Rays. The round-trip time is the time when the ultrasonic wave sent from the ultrasonic transmitter propagates through the gas medium to the receiver. The round-trip time multiplied by the speed of sound in the gas medium is the distance traveled by the sound wave, and the measured distance is half of the distance traveled by the sound wave. This distance measurement method is a non-contact distance measurement with high sensitivity, which can collect distance information in real time and provide real-time and reliable information for the relative position judgment of the vehicle body. Since the ultrasonic wave propagates in the air, the speed...
PUM
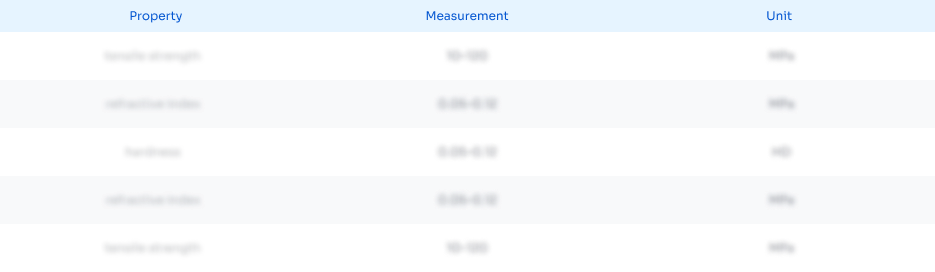
Abstract
Description
Claims
Application Information

- R&D Engineer
- R&D Manager
- IP Professional
- Industry Leading Data Capabilities
- Powerful AI technology
- Patent DNA Extraction
Browse by: Latest US Patents, China's latest patents, Technical Efficacy Thesaurus, Application Domain, Technology Topic, Popular Technical Reports.
© 2024 PatSnap. All rights reserved.Legal|Privacy policy|Modern Slavery Act Transparency Statement|Sitemap|About US| Contact US: help@patsnap.com