Preparation method of black flame-retardant PBT composite material capable of being welded by laser
A technology of laser welding and composite materials, which is applied in the field of polymer materials, can solve the problems of difficult laser welding of black PBT, achieve excellent laser welding ability, avoid strong absorption, and have good compatibility
- Summary
- Abstract
- Description
- Claims
- Application Information
AI Technical Summary
Problems solved by technology
Method used
Examples
Embodiment 1
[0039] A preparation method of laser weldable black flame-retardant PBT composite material, specifically as follows:
[0040] (1) Preparation of raw materials;
[0041] In terms of parts by mass, 70 parts of PBT TH6100 resin, 8 parts of flame retardant (di(phenoxy) polyphosphazene) (SPB100) and 0.3 parts of black powder were mixed for 2 minutes in a high-speed mixer, and the obtained mixture was used as raw material I;
[0042] The black powder is compounded by perylene-based red toner, instaline-based blue toner and isoindoline-based yellow toner with a mass ratio of 1:0.6:0.9;
[0043] In terms of parts by mass, 10 parts of PBT KH2083 resin and 0.2 parts of N-butylpiguanic acid potassium salt were mixed for 2 minutes in a high-speed mixer, and the obtained mixture was raw material II;
[0044] (2) Add raw material I to the feeding port on the main side of the twin-screw extruder, add raw material II to the feeding port on the 4th stage of the twin-screw extruder, extrude a...
Embodiment 2
[0049] A preparation method of laser weldable black flame-retardant PBT composite material, specifically as follows:
[0050] (1) Preparation of raw materials;
[0051] In terms of parts by mass, 72 parts of PBT TH6100 resin, 8 parts of flame retardant (di(phenoxy) polyphosphazene) (SPB100) and 0.5 parts of black powder were mixed for 2 minutes in a high-speed mixer, and the obtained mixture was used as the raw material I;
[0052] The black powder is compounded by perylene-based red toner, instaline-based blue toner and isoindoline-based yellow toner with a mass ratio of 1:0.6:1;
[0053] In terms of parts by mass, 12 parts of PBT KH2083 resin and 0.5 part of N-butylpiguanic acid potassium salt were mixed for 2 minutes in a high-speed mixer, and the obtained mixture was raw material II;
[0054] (2) Add raw material I to the feeding port on the main side of the twin-screw extruder, add raw material II to the feeding port on the 4th stage of the twin-screw extruder, extrude ...
Embodiment 3
[0059] A preparation method of laser weldable black flame-retardant PBT composite material, specifically as follows:
[0060] (1) Preparation of raw materials;
[0061] In terms of parts by mass, 75 parts of PBT TH6100 resin, 8 parts of flame retardant (di(phenoxy) polyphosphazene) (SPB100) and 0.7 parts of black powder were mixed for 3 minutes in a high-speed mixer, and the obtained mixture was used as the raw material I;
[0062] The black powder is compounded by perylene-based red toner, instaline-based blue toner and isoindoline-based yellow toner with a mass ratio of 1:0.6:1.1;
[0063] In terms of parts by mass, 14 parts of PBT KH2083 resin and 1 part of N-butylpiguanic acid potassium salt were mixed for 3 minutes in a high-speed mixer, and the obtained mixture was raw material II;
[0064] (2) Add raw material I to the feeding port on the main side of the twin-screw extruder, add raw material II to the feeding port on the 4th stage of the twin-screw extruder, extrude ...
PUM
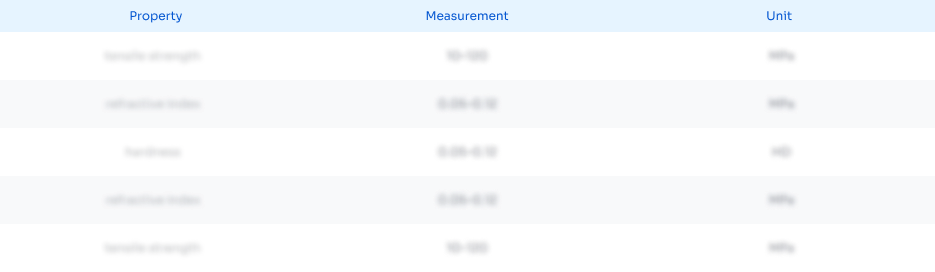
Abstract
Description
Claims
Application Information

- R&D Engineer
- R&D Manager
- IP Professional
- Industry Leading Data Capabilities
- Powerful AI technology
- Patent DNA Extraction
Browse by: Latest US Patents, China's latest patents, Technical Efficacy Thesaurus, Application Domain, Technology Topic, Popular Technical Reports.
© 2024 PatSnap. All rights reserved.Legal|Privacy policy|Modern Slavery Act Transparency Statement|Sitemap|About US| Contact US: help@patsnap.com