Environment-friendly biomass bacteriostatic wear-resistant agent and preparation method thereof
A biomass and wear-resistant agent technology, applied in textiles and papermaking, etc., can solve problems such as high irritation or toxicity, insufficient wear resistance of coatings, and insufficient environmental protection, etc., to achieve improved puncture resistance, performance improvement, and antibacterial properties and good wear resistance
- Summary
- Abstract
- Description
- Claims
- Application Information
AI Technical Summary
Problems solved by technology
Method used
Image
Examples
Embodiment 1
[0036] (1) In parts by weight, the raw materials weighed are as follows: 10 parts of straw ash water, 10 parts of rice washing water, 1 part of allicin, 1 part of chlorothalonil, 9 parts of nano-scale kaolin, 8 parts of high wear-resistant carbon black , 4 parts of nano-scale titanium dioxide, 1 part of film-forming agent, and 1 part of penetrating agent; Sodium base sulfonate; film-forming agent is protein film-forming agent, acrylic resin film-forming agent, butadiene resin film-forming agent, polyurethane film-forming agent, nitrocellulose film-forming agent in mass ratio 1:1:1:1:1 ;
[0037] (2) Add 10 parts of straw ash water, 10 parts of rice washing water, 1 part of allicin, and 1 part of chlorothalonil into the reaction kettle, stir at 800 rpm for 25 minutes until completely mixed;
[0038] (3) After being completely mixed, continue to add 9 parts of nano-scale kaolin and 8 parts of high wear-resistant carbon black in the reaction kettle, stir for 10 minutes at 800 rp...
Embodiment 2
[0042] (1) In parts by weight, the raw materials were weighed as follows: 15 parts of straw ash water, 15 parts of rice washing water, 3 parts of allicin, 1 part of chlorothalonil, 10 parts of nano-scale kaolin, 9 parts of high wear-resistant carbon black , 5 parts of nano-scale titanium dioxide, 1 part of film-forming agent, and 1 part of penetrating agent; Sodium base sulfonate; film-forming agent is protein film-forming agent, acrylic resin film-forming agent, butadiene resin film-forming agent, polyurethane film-forming agent, nitrocellulose film-forming agent in mass ratio 1:1:1:1:1 ;
[0043] (2) Add 15 parts of straw ash water, 15 parts of rice washing water, 3 parts of allicin, and 1 part of chlorothalonil into the reaction kettle, stir at 800 rpm for 25 minutes until completely mixed;
[0044] (3) After being completely mixed, continue to add 10 parts of nano-scale kaolin and 9 parts of high wear-resistant carbon black in the reaction kettle, stir for 10 minutes at 8...
Embodiment 3
[0048] (1) In parts by weight, the raw materials were weighed as follows: 20 parts of straw ash water, 20 parts of rice washing water, 5 parts of allicin, 2 parts of chlorothalonil, 13 parts of nano-scale kaolin, 10 parts of high wear-resistant carbon black , 6 parts of nano-scale titanium dioxide, 2 parts of film-forming agent, and 2 parts of penetrating agent; Sodium base sulfonate; film-forming agent is protein film-forming agent, acrylic resin film-forming agent, butadiene resin film-forming agent, polyurethane film-forming agent, nitrocellulose film-forming agent in mass ratio 1:1:1:1:1 ;
[0049] (2) Add 20 parts of straw ash water, 20 parts of rice washing water, 5 parts of allicin, and 2 parts of chlorothalonil into the reaction kettle, stir at 800 rpm for 25 minutes until completely mixed;
[0050] (3) After being completely mixed, continue to add 13 parts of nano-scale kaolin and 10 parts of high wear-resistant carbon black in the reaction kettle, stir for 10 minute...
PUM
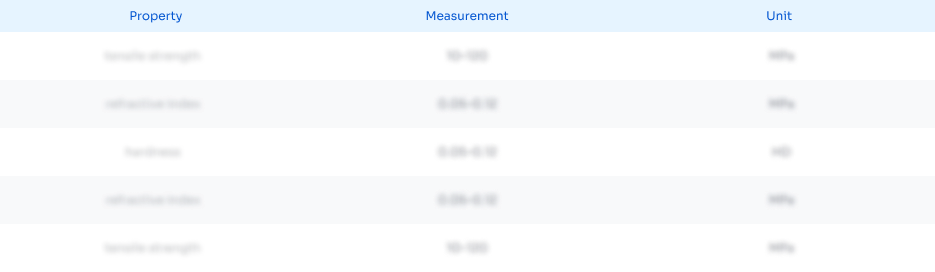
Abstract
Description
Claims
Application Information

- Generate Ideas
- Intellectual Property
- Life Sciences
- Materials
- Tech Scout
- Unparalleled Data Quality
- Higher Quality Content
- 60% Fewer Hallucinations
Browse by: Latest US Patents, China's latest patents, Technical Efficacy Thesaurus, Application Domain, Technology Topic, Popular Technical Reports.
© 2025 PatSnap. All rights reserved.Legal|Privacy policy|Modern Slavery Act Transparency Statement|Sitemap|About US| Contact US: help@patsnap.com