Method for removing iron, aluminum and silicon from nickel-cobalt-manganese-copper solution under normal pressure
A technology of nickel-cobalt-manganese-copper and iron-aluminum-silicon, applied in the field of hydrometallurgy or chemical industry, can solve the problems of high consumption of auxiliary materials, poor slag filtration, high salinity of wastewater, etc., to reduce the pressure of sewage treatment and avoid the richness of iron, aluminum and silicon The effect of collecting and reducing the salinity of wastewater
- Summary
- Abstract
- Description
- Claims
- Application Information
AI Technical Summary
Problems solved by technology
Method used
Image
Examples
Embodiment 1
[0033] 1) Take the crude cobalt hydroxide raw material, containing cobalt, nickel and manganese, and slurry it at a liquid-solid ratio of 3:1, add sulfuric acid and sodium sulfite, the pH of the leaching end point is 0.5, Fe 2+ =1.5g / L; after dense separation, the supernatant was transferred to the transfer tank, and the temperature was kept at 60°C;
[0034] 2) Take the above-mentioned cobalt manganese hydroxide raw material, add water to slurry, and configure it as a precipitant with a solid content of 20%;
[0035] 3) Using the nickel-cobalt-manganese solution after impurity removal as the base liquid, raise the temperature and maintain the temperature at 80°C. The above-mentioned supernatant and the above-mentioned precipitant are pumped into the bottom liquid in the form of parallel flow to maintain pH=4.0, and the reaction time is maintained for 2 hours by controlling the pumping speed;
[0036] 4) The above-mentioned slurry is separated from solid-liquid to obtain iron...
Embodiment 2
[0038] 1) Take the crude nickel hydroxide raw material, containing cobalt, nickel, and manganese, and slurry it with a liquid-solid ratio of 3:1, add sulfuric acid and sodium metabisulfite, and the pH of the leaching end point is 2.0, Fe 2+=0.7g / L; after dense separation, the supernatant was transferred to the transfer tank, and the temperature was kept at 70°C;
[0039] 2) Take the above-mentioned crude nickel-manganese hydroxide raw material, add water to slurry, and configure it as a precipitant with a solid content of 32%;
[0040] 3) Using the nickel-cobalt-manganese solution after impurity removal as the bottom solution, raise the temperature and maintain the temperature at 90°C. The above-mentioned supernatant and the above-mentioned precipitant are pumped into the bottom liquid in the form of parallel flow to maintain pH=3.0, and the reaction time is maintained for 4 hours by controlling the pumping speed;
[0041] 4) The above-mentioned slurry is separated from solid...
Embodiment 3
[0043] 1) Take the crude manganese carbonate raw material, containing cobalt, nickel, and manganese, and slurry it with a liquid-solid ratio of 3:1, add sulfuric acid and sodium thiosulfate, the pH of the leaching end point is 1.5, Fe 2+ =0.45g / L; after dense separation, the supernatant was transferred to the transfer tank, and the temperature was kept at 50°C;
[0044] 2) Take the above crude manganese carbonate raw material, add water to slurry, and configure it as a precipitant with a solid content of 15%;
[0045] 3) Using the nickel-cobalt-manganese solution after impurity removal as the bottom solution, raise the temperature and maintain the temperature at 90°C. The above-mentioned supernatant and the above-mentioned precipitant are pumped into the bottom liquid in the form of parallel flow to maintain pH=3.5, and the reaction time is maintained for 1.5 hours by controlling the pumping speed;
[0046] 4) The above-mentioned slurry is separated from solid-liquid to obtai...
PUM
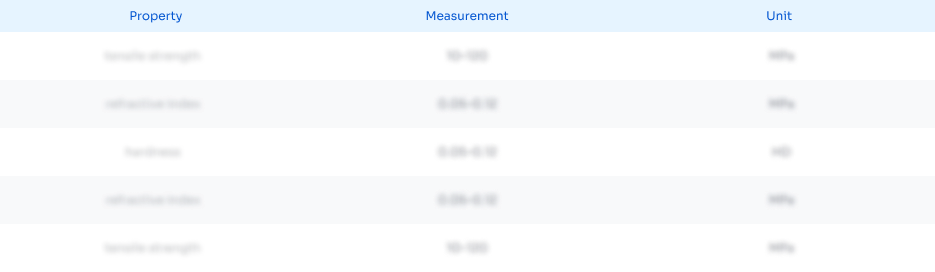
Abstract
Description
Claims
Application Information

- Generate Ideas
- Intellectual Property
- Life Sciences
- Materials
- Tech Scout
- Unparalleled Data Quality
- Higher Quality Content
- 60% Fewer Hallucinations
Browse by: Latest US Patents, China's latest patents, Technical Efficacy Thesaurus, Application Domain, Technology Topic, Popular Technical Reports.
© 2025 PatSnap. All rights reserved.Legal|Privacy policy|Modern Slavery Act Transparency Statement|Sitemap|About US| Contact US: help@patsnap.com