Forging method for improving structure performance of TC11 alloy wheel disc-journal die forging
A TC11, microstructure and performance technology, applied in the field of material thermal processing, can solve the problem that the deformation amount of the deformation area cannot meet the requirements of low-magnification structure of forgings, and achieve the effect of improving the low-magnification structure level.
- Summary
- Abstract
- Description
- Claims
- Application Information
AI Technical Summary
Problems solved by technology
Method used
Image
Examples
Embodiment 1
[0026] Example 1: The structure of the forging should reach grade 1-2.
[0027] The first step: Die forging first fire production:
[0028] The preform is forged after being held at 40°C for 270 minutes at the phase transition point. The heating coefficient is 0.8min / mm. After the holding time is up, the die forging production is carried out. This process needs to control key parameters such as initial forging temperature and final forging temperature, vertical size, etc. . According to previous simulation calculations, this fire can well control the deformation of the center of the forging. H forging to 200mm can control the deformation of the center within 34%, reducing the tendency of the center metal to flow too fast.
[0029] The second step: Die forging Second fire production:
[0030] After the die forging is completed, the forgings are air-cooled. After sand blowing and grinding, the second fire is produced. The preform after the first fire is forged at the phase t...
Embodiment 2
[0033] Embodiment 2: The forging structure should reach: 3-4 grades.
[0034] The first step: Die forging first fire production:
[0035] The preform is forged after being held at 40°C for 270 minutes at the phase transition point. The heating coefficient is 0.8min / mm. After the holding time is up, the die forging production is carried out. This process needs to control key parameters such as initial forging temperature and final forging temperature, vertical size, etc. . According to previous simulation calculations, this fire can well control the deformation of the center of the forging. H forging to 200mm can control the deformation of the center within 34%, reducing the tendency of the center metal to flow too fast.
[0036] The second step: Die forging Second fire production:
[0037] After the die forging is completed, the forgings are air-cooled. After sand blowing and grinding, the second fire is produced. The preform after the first fire is forged at the phase tra...
Embodiment 3
[0040] Embodiment 3: Forging structure should reach: 5-6 grades.
[0041] The first step: Die forging first fire production:
[0042] The preform is forged after being held at 40°C for 270 minutes at the phase transition point. The heating coefficient is 0.8min / mm. After the holding time is up, the die forging production is carried out. This process needs to control key parameters such as initial forging temperature and final forging temperature, vertical size, etc. . According to previous simulation calculations, this fire can well control the deformation of the center of the forging. H forging to 200mm can control the deformation of the center within 34%, reducing the tendency of the center metal to flow too fast.
[0043] The second step: Die forging Second fire production:
[0044] After the die forging is completed, the forgings are air-cooled. After sand blowing and grinding, the second fire is produced. The preform after the first fire is forged at the phase transit...
PUM
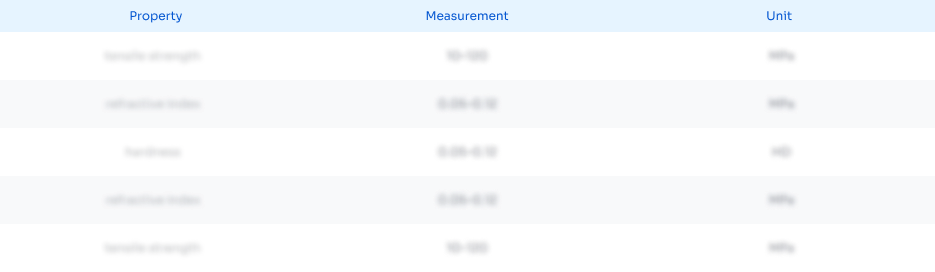
Abstract
Description
Claims
Application Information

- R&D Engineer
- R&D Manager
- IP Professional
- Industry Leading Data Capabilities
- Powerful AI technology
- Patent DNA Extraction
Browse by: Latest US Patents, China's latest patents, Technical Efficacy Thesaurus, Application Domain, Technology Topic, Popular Technical Reports.
© 2024 PatSnap. All rights reserved.Legal|Privacy policy|Modern Slavery Act Transparency Statement|Sitemap|About US| Contact US: help@patsnap.com