Device and method for machining groove profile of wear-resistant rolling roller sleeve
A technology for machining grooves and roller sleeves, which is used in grinding drive devices, metal processing equipment, and parts of grinding machine tools, etc. It can solve problems such as the inability to meet the diverse needs of groove shapes, poor outer circle consistency, and difficult machining.
- Summary
- Abstract
- Description
- Claims
- Application Information
AI Technical Summary
Problems solved by technology
Method used
Image
Examples
Embodiment 1
[0054] Specifications of wear-resistant rolling roller cover: φ1600mm / φ1050mm×1000mm, outer circular groove type requires flute width / groove width*depth=20mm / 15mm*7mm.
[0055] The specific processing steps are as follows:
[0056] S1. Confirm the outer circle of the wear-resistant rolling roller sleeve 4: use a caliper to measure and confirm the outer circle size of the wear-resistant rolling roller sleeve 4: φ1600±0.5mm, outer cylindricity≤0.5, roughness Ra=6.3;
[0057] S2. Scribing and punching holes on the wear-resistant roller cover 4: the number of grooves to be processed N the number of grooves=1600×π / (20+15)=143.61, and the number of grooves is 144;
[0058] Apply the color paste within 10 mm of the outer circular end face, and divide it into 12 equal parts along the axial surface and radial surface of the outer circle of the wear-resistant roller sleeve 4, and use a punch to punch holes at the crossing points of the marking lines;
[0059] S3. Place the wear-resista...
PUM
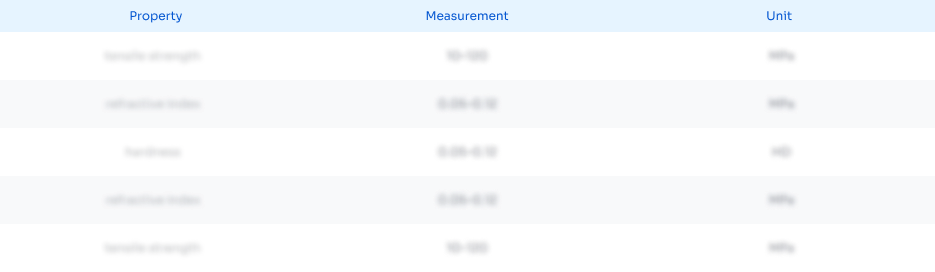
Abstract
Description
Claims
Application Information

- R&D Engineer
- R&D Manager
- IP Professional
- Industry Leading Data Capabilities
- Powerful AI technology
- Patent DNA Extraction
Browse by: Latest US Patents, China's latest patents, Technical Efficacy Thesaurus, Application Domain, Technology Topic, Popular Technical Reports.
© 2024 PatSnap. All rights reserved.Legal|Privacy policy|Modern Slavery Act Transparency Statement|Sitemap|About US| Contact US: help@patsnap.com