Novel preparation method of spinel type composite oxide MnCo2O4
A composite oxide and spinel-type technology, applied in the direction of metal/metal oxide/metal hydroxide catalysts, chemical instruments and methods, chemical/physical processes, etc., can solve the problems of high gelation temperature and long time , to achieve the effect of low roasting temperature, high combustion heat and lower roasting temperature
- Summary
- Abstract
- Description
- Claims
- Application Information
AI Technical Summary
Problems solved by technology
Method used
Examples
Embodiment 1
[0022] The preparation of MnCo mentioned in the present invention 2 o 4 The spontaneous combustion method of the spinel type composite oxide catalyst is as follows:
[0023] First, weigh 4.9 g of manganese acetate tetrahydrate and place it in a mortar, and grind for 5 minutes; then weigh 11.64 g of cobalt nitrate hexahydrate, and grind for 5 minutes; mix the two substances and continue grinding for 5 minutes. Weigh 6.48g of glucose according to a certain proportion and grind it for 5 minutes; mix the ground glucose and metal salt and continue grinding for 25 minutes to obtain a pink viscous compound intermediate; then put it in an oven at 160°C for 12 hours, and burn it to get gray fluffy powder The final sample precursor is roasted in a muffle furnace under the following conditions: in air at a rate of 5 °C / min from room temperature to 500 °C, constant temperature for 4 hours, and naturally lowered to room temperature to obtain MnCo 2 o 4 spinel composite oxide.
[0024] ...
Embodiment 2
[0027] The preparation of MnCo mentioned in the present invention 2 o 4 The spontaneous combustion method of the spinel type composite oxide catalyst is as follows:
[0028] Firstly, weigh 4.9 g of manganese acetate tetrahydrate and place it in a mortar, and grind for 10 minutes; then weigh 11.64 g of cobalt nitrate hexahydrate, and grind for 10 minutes; mix the two substances and continue grinding for 5 minutes. Weigh 8.64g of glucose according to a certain proportion and grind it for 5 minutes; mix the ground glucose and metal salt and continue grinding for 25 minutes to obtain a pink viscous compound intermediate; then put it in an oven at 180°C for 24 hours, and burn it to get gray fluffy powder The final sample precursor is roasted in a muffle furnace under the following conditions: in air at a rate of 5 °C / min from room temperature to 500 °C, constant temperature for 6 hours, and naturally lowered to room temperature to obtain MnCo 2 o 4 spinel composite oxide.
[00...
Embodiment 3
[0032] The preparation of MnCo mentioned in the present invention 2 o 4 The spontaneous combustion method of the spinel type composite oxide catalyst is as follows:
[0033]First, weigh 5.6g of manganese acetate tetrahydrate and place it in a mortar, and grind for 5 minutes; then weigh 12.81g of cobalt nitrate hexahydrate, and grind for 5 minutes; mix the two substances and continue grinding for 5 minutes. Weigh 7.68g of glucose according to a certain proportion and grind it for 5 minutes; mix the ground glucose and metal salt and continue grinding for 25 minutes to obtain a pink viscous compound intermediate; then put it in an oven at 160°C for 18 hours, and burn it to get gray fluffy powder The final sample precursor is roasted in a muffle furnace under the following conditions: in air at a rate of 5 °C / min from room temperature to 500 °C, constant temperature for 4 hours, and naturally lowered to room temperature to obtain MnCo 2 o 4 spinel composite oxide.
[0034] Eva...
PUM
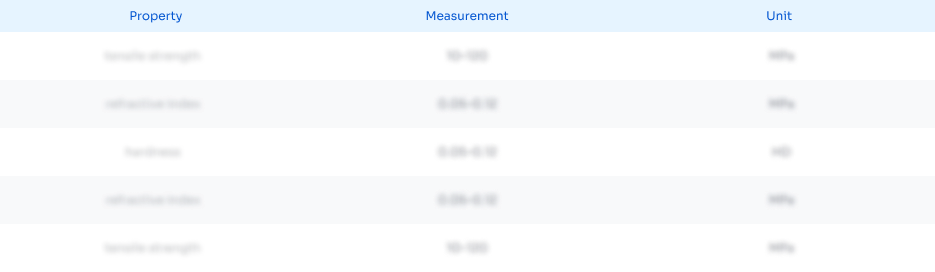
Abstract
Description
Claims
Application Information

- R&D
- Intellectual Property
- Life Sciences
- Materials
- Tech Scout
- Unparalleled Data Quality
- Higher Quality Content
- 60% Fewer Hallucinations
Browse by: Latest US Patents, China's latest patents, Technical Efficacy Thesaurus, Application Domain, Technology Topic, Popular Technical Reports.
© 2025 PatSnap. All rights reserved.Legal|Privacy policy|Modern Slavery Act Transparency Statement|Sitemap|About US| Contact US: help@patsnap.com