Pressing and cutting head for transfer film
A transfer film and cutting head technology, which is applied in metal processing and other directions, can solve problems such as troublesome transfer film sticking to the cutter, and achieve the effect of reducing the defect rate and enhancing stability
- Summary
- Abstract
- Description
- Claims
- Application Information
AI Technical Summary
Problems solved by technology
Method used
Image
Examples
Embodiment Construction
[0018] see Figure 1 to Figure 4 , a press cutting head for a transfer film of the present invention includes a cutter head top plate 71, a cutter head driver 72, a cutter head bottom plate 73, a blade 74, a partition box 75 and a support rod 76, and the two ends of several said support rods 76 They are respectively connected with the cutter head top plate 71 and the partition box 75. The cutter head bottom plate 73 is located between the cutter head top plate 71 and the partition box 75 and is driven up and down by the cutter head driver 72. The top of the blade 74 is connected to the cutter head bottom plate. 73 are connected to each other and the bottom end is arranged through the partition box 75. The bottom surface of the partition box 75 and located on the left and right sides of the blade 74 are respectively provided with several bumps 752. The blade driver 72 includes a blade screw 721, A cutter head motor 722 and a cutter head screw nut 723, the cutter head motor 722 ...
PUM
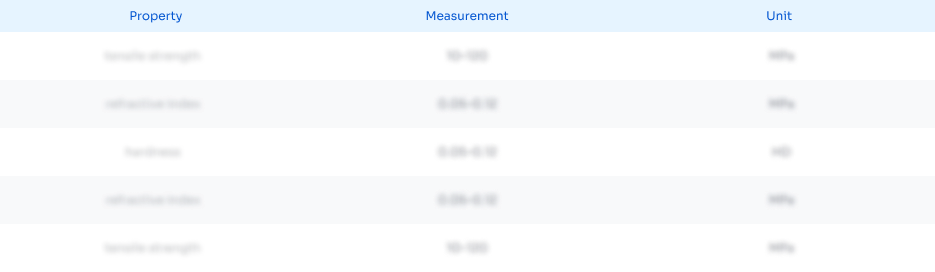
Abstract
Description
Claims
Application Information

- Generate Ideas
- Intellectual Property
- Life Sciences
- Materials
- Tech Scout
- Unparalleled Data Quality
- Higher Quality Content
- 60% Fewer Hallucinations
Browse by: Latest US Patents, China's latest patents, Technical Efficacy Thesaurus, Application Domain, Technology Topic, Popular Technical Reports.
© 2025 PatSnap. All rights reserved.Legal|Privacy policy|Modern Slavery Act Transparency Statement|Sitemap|About US| Contact US: help@patsnap.com