Slotless direct-current hybrid magnetic bearing
A hybrid magnetic bearing and winding technology, used in magnetic bearings, bearings, shafts and bearings, etc., can solve the problems of long axial length, large radial magnetic pole area, and occupying radial space.
- Summary
- Abstract
- Description
- Claims
- Application Information
AI Technical Summary
Problems solved by technology
Method used
Image
Examples
Embodiment approach 1
[0024] Specific implementation methods such as Figure 1-6As shown, the present invention discloses a slotless DC hybrid magnetic bearing, which includes a stator and a rotor. The stator includes a left stator core 1 , a right stator core 2 and a permanent magnet ring 3 . The two stator cores are disc ring structures; the permanent magnet ring 3 is axially magnetized, and the outer diameter of the permanent magnet ring 3 is the same as that of the two stator cores, and the two stator cores are the left stator core 1 and the left stator core respectively. The right stator core 2, the left stator core 1 and the right stator core 2 are connected through the permanent magnet ring 3. The rotor includes a rotor core 4 and a rotating shaft 5. The rotor core 4 is a ring structure, and the rotating shaft 5 runs through the rotor core 4. The rotor core 4 has an "H"-shaped structure along the radial section. The left and right sides of the rotor core 4 are respectively connected to the l...
Embodiment approach 2
[0034] The difference between this embodiment and Embodiment 1 is that both sides of the rotor core 4 are connected to commutators, that is, when there are two commutators, the winding R l1 -R l12 , R r1 -R r12 For suspension control, the winding relative to the 4 circular inner slots of the rotor core: Winding R l1 with R l7 , Winding R l2 with R l8 , Winding R l3 with R l9 , Winding R l4 with R l10 , Winding R l5 with R l11 , Winding R l6 with R l12 , Winding R r1 with R r7 , Winding R r2 with R r8 , Winding R r3 with R r9 , Winding R r4 with R r10 , Winding R r5 with R r11 , Winding R r6 with R r12 In series in the same direction, one end of the 12 windings on the left is connected to the 12 commutator segments 9 in the left commutator, one end of the 12 windings on the right is connected to the 12 commutator segments 9 in the right commutator, each 3 Each commutator segment 9 corresponds to one carbon brush 10 , and each commutator is provided with...
PUM
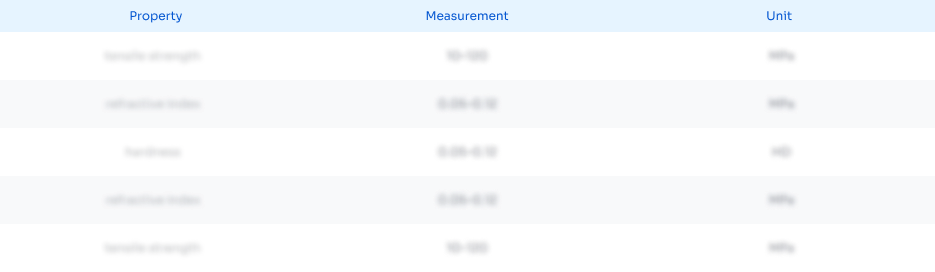
Abstract
Description
Claims
Application Information

- R&D Engineer
- R&D Manager
- IP Professional
- Industry Leading Data Capabilities
- Powerful AI technology
- Patent DNA Extraction
Browse by: Latest US Patents, China's latest patents, Technical Efficacy Thesaurus, Application Domain, Technology Topic, Popular Technical Reports.
© 2024 PatSnap. All rights reserved.Legal|Privacy policy|Modern Slavery Act Transparency Statement|Sitemap|About US| Contact US: help@patsnap.com