Preparation method of selective laser melting formed nano TiB2 reinforced aluminum-based composite material
A technology of laser selective melting and composite materials, which is applied in nanotechnology, nanotechnology, nanotechnology for materials and surface science, etc. It can solve the problems of low laser absorption rate, high viscosity of metal solution, and poor fluidity
- Summary
- Abstract
- Description
- Claims
- Application Information
AI Technical Summary
Problems solved by technology
Method used
Image
Examples
Embodiment 1
[0024] A Laser Selective Melting Nano-TiB 2 Particle-reinforced aluminum matrix composite material, the preparation method is as follows:
[0025] Step 1: The mixed powder has a purity > 99.9%, a particle size of 15-53 μm, and a shape of high-purity spherical AlSi10Mg powder, and a purity > 99.9%, a particle size of 50-100 nm, and a shape of TiB with an irregular structure. 2 Powder composition, TiB in mixed powder 2 The mass fraction is 1wt.%, figure 1 is the composite powder morphology after powder mixing;
[0026] Step 2: Put the mixed powder in step (1) into the mixing cylinder. For powder mixing, rotate forward for 30 minutes at a speed of 12 rpm, reverse for 30 minutes at a speed of 12 rpm, repeat the above steps once, and blend the powder for 120 minutes.
[0027] Step 3: put the mixed composite powder into the oven, the temperature of the powder is 120°C, the time of the powder is 3 hours, and it is cooled with the furnace.
[0028] Step 4: Establish a three-dimen...
Embodiment 2
[0032] A Laser Selective Melting Nano-TiB 2 Particle-reinforced aluminum matrix composite material, the preparation method is as follows:
[0033] Step 1: The mixed powder has a purity > 99.9%, a particle size of 15-53 μm, and a shape of high-purity spherical AlSi10Mg powder, and a purity > 99.9%, a particle size of 50-100 nm, and a shape of TiB with an irregular structure. 2 Powder composition, TiB in mixed powder 2 The mass fraction of is 2wt.%.
[0034] Step 2: Put the mixed powder in step (1) into the mixing cylinder. Mix the powder by rotating forward for 50min at a speed of 12rpm, reverse for 50min at a speed of 12rpm, repeat the above steps once, and blend the powder for 200min.
[0035] Step 3: put the mixed composite powder into the oven, the temperature of the powder is 120°C, the time of the powder is 3 hours, and it is cooled with the furnace.
[0036] Step 4: Establish a three-dimensional digital model of the sample to be processed, and use layering software t...
Embodiment 3
[0040] A Laser Selective Melting Nano-TiB 2 Particle-reinforced aluminum matrix composite material, the preparation method is as follows:
[0041] Step 1: The mixed powder has a purity > 99.9%, a particle size of 15-53 μm, and a shape of high-purity spherical AlSi10Mg powder, and a purity > 99.9%, a particle size of 50-100 nm, and a shape of TiB with an irregular structure. 2 Powder composition, TiB in mixed powder 2 The mass fraction of is 3wt.%.
[0042] Step 2: Put the mixed powder in step (1) into the mixing cylinder. For powder mixing, rotate forward for 70 minutes at a speed of 12 rpm, reverse for 70 minutes at a speed of 12 rpm, repeat the above steps once, and blend the powder for 280 minutes.
[0043] Step 3: put the mixed composite powder into the oven, the temperature of the powder is 120°C, the time of the powder is 3 hours, and it is cooled with the furnace.
[0044] Step 4: Establish a three-dimensional digital model of the sample to be processed, and use layer...
PUM
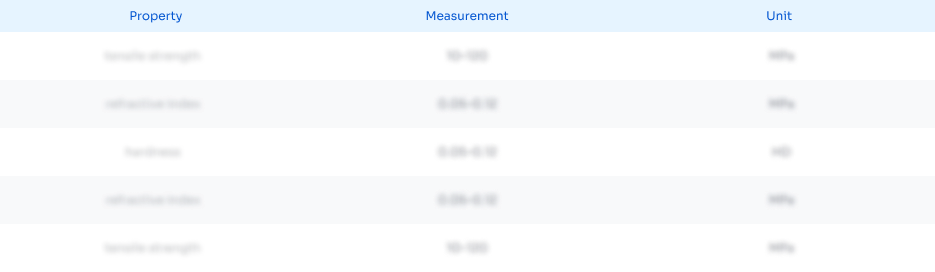
Abstract
Description
Claims
Application Information

- R&D
- Intellectual Property
- Life Sciences
- Materials
- Tech Scout
- Unparalleled Data Quality
- Higher Quality Content
- 60% Fewer Hallucinations
Browse by: Latest US Patents, China's latest patents, Technical Efficacy Thesaurus, Application Domain, Technology Topic, Popular Technical Reports.
© 2025 PatSnap. All rights reserved.Legal|Privacy policy|Modern Slavery Act Transparency Statement|Sitemap|About US| Contact US: help@patsnap.com