Lithium iron phosphate waste recovery method and application thereof
A recycling method and technology for lithium iron phosphate, applied in the field of recycling lithium iron phosphate waste, can solve the problems of low recovery rate of key element lithium and high energy consumption, etc.
- Summary
- Abstract
- Description
- Claims
- Application Information
AI Technical Summary
Problems solved by technology
Method used
Image
Examples
Embodiment 1
[0038] The recovery method of the lithium iron phosphate waste material of the present embodiment may further comprise the steps:
[0039] (1) dismantling, crushing and sieving the lithium iron phosphate waste to obtain lithium iron phosphate powder;
[0040] (2) Weigh 500g of lithium iron phosphate powder with a mass fraction of 67.7%, configure 3000ml of NaOH solution with a mass fraction of 10%, and mix to obtain a lithium iron phosphate slurry;
[0041] (3) Place the slurry obtained in step (2) in a constant temperature water bath at a temperature of 80° C., feed air, react for 120 minutes, filter to obtain 2887 ml of lye containing sodium metaaluminate and sodium phosphate, and obtain lithium phosphate, 409.2 grams of slag material of carbon powder and ferric oxide;
[0042] (4) Take step (3) slag material 300g of lithium phosphate, carbon powder and ferric oxide, configure 2400ml mass fraction of 10% ammonia solution, mix under nitrogen atmosphere to obtain lithium phos...
Embodiment 2
[0047] The recovery method of the lithium iron phosphate waste material of the present embodiment may further comprise the steps:
[0048] (1) dismantling, crushing and sieving the lithium iron phosphate waste to obtain lithium iron phosphate powder;
[0049] (2) Weigh 500g of lithium iron phosphate powder with a mass fraction of 67.7%, configure 3000ml of NaOH solution with a mass fraction of 12%, and mix to obtain a lithium iron phosphate slurry;
[0050] (3) Place the slurry obtained in step (2) in a constant temperature water bath at a temperature of 80° C., feed air, react for 120 minutes, filter to obtain 2905 ml of lye containing sodium metaaluminate and sodium phosphate, and obtain lithium phosphate, 408.8 grams of slag material of carbon powder and ferric oxide;
[0051] (4) Take step (3) slag material 300g of lithium phosphate, carbon powder and ferric oxide, configure 2400ml mass fraction 8% ammonia solution, mix under nitrogen atmosphere to obtain lithium phosphat...
Embodiment 3
[0055] The recovery method of the lithium iron phosphate waste material of the present embodiment may further comprise the steps:
[0056] (1) dismantling, crushing and sieving the lithium iron phosphate waste to obtain lithium iron phosphate powder;
[0057] (2) Weigh 500g of lithium iron phosphate powder with a mass fraction of 67.7%, configure 2500ml of NaOH solution with a mass fraction of 5%, and mix to obtain a lithium iron phosphate slurry;
[0058] (3) Place the slurry obtained in step (2) in a constant temperature water bath at a temperature of 80° C., react for 90 minutes, filter to obtain 2412 ml of lye containing sodium metaaluminate, and obtain 473.1 ml of slag containing lithium iron phosphate and carbon powder gram;
[0059] (4) Get the leach solution and lithium iron phosphate slag obtained in step (3), carry out processes such as dilution and slag, and obtain the leaching rates of aluminum, phosphorus, and lithium to be 70.8%, 2.47%, and 2.82%, respectively. ...
PUM
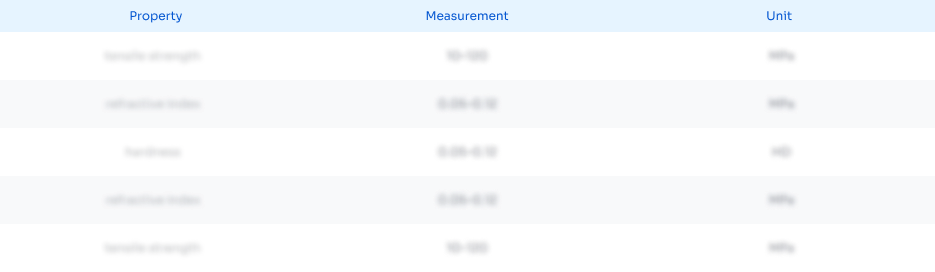
Abstract
Description
Claims
Application Information

- Generate Ideas
- Intellectual Property
- Life Sciences
- Materials
- Tech Scout
- Unparalleled Data Quality
- Higher Quality Content
- 60% Fewer Hallucinations
Browse by: Latest US Patents, China's latest patents, Technical Efficacy Thesaurus, Application Domain, Technology Topic, Popular Technical Reports.
© 2025 PatSnap. All rights reserved.Legal|Privacy policy|Modern Slavery Act Transparency Statement|Sitemap|About US| Contact US: help@patsnap.com