Fluorine-free treatment agent, oil-proof paper and food packaging material
A technology of fluorine treatment and additives, applied in the field of functional materials, can solve problems such as poor oil resistance, unfavorable industrial production, and high viscosity
- Summary
- Abstract
- Description
- Claims
- Application Information
AI Technical Summary
Problems solved by technology
Method used
Image
Examples
Embodiment 1
[0088] A fluorine-free treatment agent, comprising: a first acrylonitrile copolymer; a second acrylonitrile copolymer; and an auxiliary agent;
[0089] Wherein, the weight ratio of the first acrylonitrile copolymer to the second acrylonitrile copolymer is 1:0.8-1.2.
[0090] (1) In the embodiment of the present invention, the synthesis method of the first acrylonitrile copolymer is:
[0091] ①Based on the total mass of the first acrylonitrile copolymer, take 0.5-8% by mass of emulsifier and 25-40% by mass of deionized water into the emulsification reactor, stir and mix and add 10-15% by mass % of the first monomer acrylonitrile monomer, 5-18 mass % of the second monomer acrylate monomer, 3-12 mass % of the third monomer vinyl aromatic monomer or olefin monomer, emulsification 0.5 h~1.0h to obtain a pre-emulsion; wherein the ratio of the first monomer acrylonitrile monomer, the second monomer acrylate monomer and the third monomer vinyl aromatic monomer or olefin monomer is 1:...
Embodiment 2
[0099] Synthesis of the first acrylonitrile copolymer:
[0100] Add 1.3g of emulsifier alkylene glycol polyether and 29.5g of deionized water into the emulsification reaction kettle, stir and mix well and add 15g of acrylonitrile monomer, 10g of 2-ethylhexyl acrylate, 12g of acetic acid Vinyl ester monomer, emulsified for 1.0h to obtain a pre-emulsion;
[0101] Add 29.5g of deionized water and 1.3g of polyethylene glycol into the reaction kettle, stir for 1h, heat up to 70°C, add 10% of the total weight of the pre-emulsion, add 0.14g of initiator potassium persulfate at the same time, and heat up to 80°C ℃, react for 0.5h, when the emulsion is bluish, slowly add the remaining pre-emulsion and 1.26g of potassium persulfate, the addition time is controlled at 3h, after the addition is completed, the temperature is raised to 90°C, and the reaction is continued for 2h, then the temperature is lowered to 40°C, and filtered Finally, the glass transition temperature and weight-avera...
Embodiment 3
[0103] Synthesis of the first acrylonitrile copolymer:
[0104] Add 2.4g of emulsifier ethoxylated castor oil and 29.1g of deionized water into the emulsification reactor, stir and mix well and add 15g of acrylonitrile monomer, 10g of cyclohexyl methacrylate, 6g of ethylene monomer, 6g of 1-methylvinylbenzene was emulsified for 1.0h to obtain a pre-emulsion;
[0105] Add 29.1g of deionized water and 1g of sodium lauryl sulfate into the reaction kettle, stir for 1h, heat up to 70°C, add 10% of the total weight of the pre-emulsion, add 0.14g of initiator potassium persulfate at the same time, and heat up to 80°C, react for 0.5h, when the emulsion is bluish, slowly add the remaining pre-emulsion and 1.26g of potassium persulfate, the addition time is controlled at 4h, after the addition is completed, the temperature is raised to 90°C, and the reaction is continued for 2h, and then the temperature is lowered to 30°C. After filtering, the glass transition temperature and weight av...
PUM
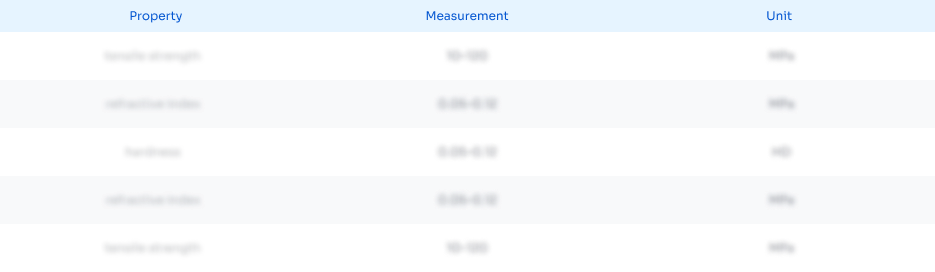
Abstract
Description
Claims
Application Information

- R&D
- Intellectual Property
- Life Sciences
- Materials
- Tech Scout
- Unparalleled Data Quality
- Higher Quality Content
- 60% Fewer Hallucinations
Browse by: Latest US Patents, China's latest patents, Technical Efficacy Thesaurus, Application Domain, Technology Topic, Popular Technical Reports.
© 2025 PatSnap. All rights reserved.Legal|Privacy policy|Modern Slavery Act Transparency Statement|Sitemap|About US| Contact US: help@patsnap.com