Nitrogen-doped carbon foam prepared by carbonizing polyester and preparation method thereof
A nitrogen-doped carbon and polyester technology, applied in the field of nitrogen-doped carbon foam and its preparation, can solve the problems of high energy consumption, high carbonization temperature, and complicated preparation process, so as to avoid reaction conditions, reduce carbonization temperature, and prepare The effect of simple process
- Summary
- Abstract
- Description
- Claims
- Application Information
AI Technical Summary
Problems solved by technology
Method used
Image
Examples
Embodiment 1
[0038] A nitrogen-doped carbon foam prepared by carbonizing polyester is prepared according to the following method:
[0039] (1) Weigh 1.5g polyethylene terephthalate (produced by Shandong Youso Chemical Co., Ltd.), 0.75g melamine (Sinopharm Chemical Reagent Co., Ltd.), 1.26g sodium chloride (Sinopharm Chemical Reagent Co., Ltd. company) and 1.74g zinc chloride (Shanghai Lingfeng Chemical Reagent Co., Ltd.), placed in a ball mill and stirred until uniformly mixed.
[0040] (2) Put the mixture obtained in step (1) into a crucible, then put it into a muffle furnace to heat up, set the muffle furnace at a heating rate of 10°C / min, and raise it to a carbonization temperature of 340°C to obtain carbonization product, and the carbonized product is obtained after separating the molten salt.
[0041] The prepared carbonized products such as figure 1 (a) shown. The product is carbon black, indicating that polyethylene terephthalate, melamine, and molten salt have been completely ca...
Embodiment 2
[0043] The 0.75g of melamine in Example 1 was replaced with 1.125g, and the other steps remained unchanged to obtain a carbonized product of polyethylene terephthalate, melamine and molten salt.
[0044] The prepared carbonized products such as figure 1 (b) shown. The product is carbon black, indicating that polyethylene terephthalate, melamine and molten salt have been completely carbonized under this condition.
Embodiment 3
[0046] The 0.75 g of melamine in Example 1 was replaced by 1.5 g, and other steps remained unchanged to obtain a carbonized product of polyethylene terephthalate, melamine and molten salt.
[0047] The prepared carbonized products such as figure 1 (c) shown. The product is carbon black, indicating that polyethylene terephthalate, melamine and molten salt have been completely carbonized under this condition.
PUM
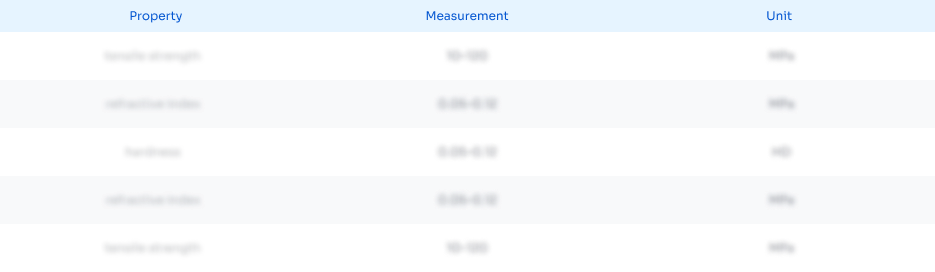
Abstract
Description
Claims
Application Information

- R&D
- Intellectual Property
- Life Sciences
- Materials
- Tech Scout
- Unparalleled Data Quality
- Higher Quality Content
- 60% Fewer Hallucinations
Browse by: Latest US Patents, China's latest patents, Technical Efficacy Thesaurus, Application Domain, Technology Topic, Popular Technical Reports.
© 2025 PatSnap. All rights reserved.Legal|Privacy policy|Modern Slavery Act Transparency Statement|Sitemap|About US| Contact US: help@patsnap.com