Method for preparing high-stability fuel cell catalyst coating slurry
A fuel cell, high-stability technology, used in battery electrodes, circuits, electrical components, etc., can solve the problem of large differences in the performance of catalyst coating membranes, and achieve the effects of avoiding damage, improving performance, and improving stability.
- Summary
- Abstract
- Description
- Claims
- Application Information
AI Technical Summary
Problems solved by technology
Method used
Image
Examples
Embodiment 1
[0024] (1) Mixing and dispersing steps for the first time:
[0025] (1) According to catalyst: surfactant: perfluorosulfonic acid resin solution: n-propanol: water = 1: 0.005: 0.25: 1: 11, take raw materials and pre-disperse the above raw materials: first weigh 110.0g of water in a beaker , and the water was placed under an electric stirrer and stirred at a stirring rate of 300rpm; while stirring, 10g of Tec10F50e catalyst produced by Tanaka Precious Metals (TKK) was slowly added to the beaker, and after stirring for 1min, 0.05g of surfactant was added in turn Sodium dodecylbenzenesulfonate, 2.5g ChemoursD2020 perfluorosulfonic acid resin solution (the solid content of the solution is 20.0%), 10.0g n-propanol; after the addition of the raw materials, continue to stir for 5.0min to fully mix the raw materials to obtain the first a predispersion.
[0026] (2) Put the first pre-dispersion in (1) into a bead mill for dispersion at a speed of 3000 rpm, and take out the slurry afte...
Embodiment 2
[0034] (1) Mixing and dispersing steps for the first time:
[0035] (1) According to catalyst: surfactant: perfluorosulfonic acid resin solution: n-propanol: water = 1: 0.005: 0.75: 1: 11 to take raw materials, and pre-disperse the above raw materials: first weigh 110.0g of water in a beaker , and the water was placed under an electric stirrer and stirred at a stirring rate of 300rpm; while stirring, 10g of Tec10F50e catalyst produced by Tanaka Precious Metals (TKK) was slowly added to the beaker, and after stirring for 1min, 0.05g of surfactant was added in turn Perfluorooctane sulfonic acid, 7.5g Chemours D2020 perfluorosulfonic acid resin solution (the solid content of the solution is 20.0%), 10.0g n-propanol; after the addition of the raw materials, continue to stir for 5.0min to fully mix the raw materials to obtain the first Predispersion.
[0036] (2) Put the first pre-dispersion in (1) into a bead mill for dispersion at a speed of 3000 rpm, and take out the slurry after...
Embodiment 3
[0044] (1) Mixing and dispersing steps for the first time:
[0045] (1) According to the catalyst: perfluorosulfonic acid resin solution: n-propanol: water = 1:0.75:1:11 to take the raw materials, and pre-disperse the above raw materials: first weigh 110.0g of water in a beaker, and put the water in Stir under an electric stirrer at a stirring rate of 300rpm; while stirring, slowly add 10g of Tec10F50e catalyst produced by Tanaka Precious Metals (TKK) in the beaker, and after stirring for 1min, add 7.5g of Chemours D2020 perfluorosulfonic acid resin solution ( The solid content of the solution is 20.0%), 10.0 g of n-propanol; after the raw materials are added, continue to stir for 5.0 min to fully mix the raw materials to obtain the first pre-dispersion.
[0046] (2) Put the first pre-dispersion in (1) into a bead mill for dispersion at a speed of 3000 rpm, and take out the slurry after grinding for 30 minutes to obtain the first-stage mixed dispersion.
[0047] (2) mixing an...
PUM
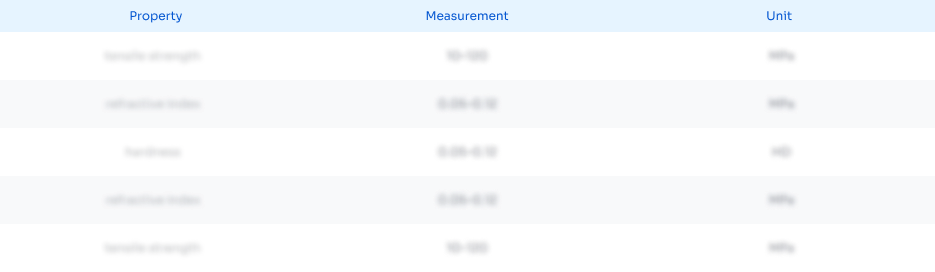
Abstract
Description
Claims
Application Information

- R&D
- Intellectual Property
- Life Sciences
- Materials
- Tech Scout
- Unparalleled Data Quality
- Higher Quality Content
- 60% Fewer Hallucinations
Browse by: Latest US Patents, China's latest patents, Technical Efficacy Thesaurus, Application Domain, Technology Topic, Popular Technical Reports.
© 2025 PatSnap. All rights reserved.Legal|Privacy policy|Modern Slavery Act Transparency Statement|Sitemap|About US| Contact US: help@patsnap.com