Molten slag viscosity prediction method based on melt structure analysis
A technology of structure analysis and prediction method, applied in the direction of prediction, analysis of materials, measurement devices, etc., can solve the problems of not considering the viscosity of slag, not having applicability, etc., and achieve the effect of great applicable value and accurate viscosity prediction
- Summary
- Abstract
- Description
- Claims
- Application Information
AI Technical Summary
Problems solved by technology
Method used
Image
Examples
Embodiment 1
[0056] Sample preparation: choose CaO, SiO 2 、Al 2 o 3 , MgO chemically pure reagent, by changing CaO / SiO 2 Ratio and Al 2 o 3 The samples to be tested were prepared separately and recorded as CSAM1~CSAM5 respectively. The specific components of the experimental slag are shown in Table 1. The specific preparation method is as follows:
[0057] Table 1 CaO-SiO 2 -Al 2 o 3 -MgO system experimental slag composition (mass fraction, %)
[0058]
[0059] 101. Combine CaO and SiO 2 、Al 2 o 3 , MgO pure reagents were calcined at 600°C for later use.
[0060] 102. Weigh 3g of mixed chemical reagents as shown in Table 1, put them into a platinum crucible, and hang them in a high-temperature quenching furnace with a molybdenum wire, then feed 0.8L / min high-purity argon gas, and heat up to the target temperature Keep warm for 2 hours. After the heat preservation is over, loosen the molybdenum wire and complete the water quenching.
[0061] 103. Take out the water-quenched ...
Embodiment 2
[0096] Sample preparation: choose CaO, MgO, SiO 2 , FeC 2 o 4 2H 2 O.P 2 o 5 Chemically pure reagents by changing CaO / SiO 2 Ratio, FeC 2 o 4 2H 2 O and P 2 o 5 The samples to be tested were prepared respectively and recorded as CMSFP1~CMSFP5. The specific components of the experimental slag are shown in Table 2. The specific preparation method is as follows:
[0097] Table 2 CaO-MgO-SiO 2 -Fe x O-P 2 o 5 Composition of experimental slag (mass fraction, %)
[0098]
[0099]
[0100] 101. Combine CaO, MgO, SiO 2 , FeC 2 o 4 2H 2 O.P 2 o 5 Pure reagents were calcined at 600°C for later use.
[0101] 102. Weigh 3g of mixed chemical reagents as shown in Table 2, put them into a platinum crucible, and hang them in a high-temperature quenching furnace with a molybdenum wire, then feed 0.8L / min high-purity argon gas, and heat up to the target temperature Keep warm for 3 hours. After the heat preservation is over, loosen the molybdenum wire and complete the ...
Embodiment 3
[0138] Sample preparation: choose CaO, SiO 2 、Al 2 o 3 , FeC 2 o 4 2H 2 O chemically pure reagent, by changing CaO / SiO 2 Ratio and Fe x O, Al 2 o 3 The samples to be tested were prepared separately and recorded as CSAF1~CSAF10 respectively. The specific components of the experimental slag are shown in Table 3. The specific preparation method is as follows:
[0139] Table 3 CaO-SiO 2 -Al 2 o 3 -Fe x Composition of O-based experimental slag (mass fraction, %)
[0140]
[0141] 101. Combine CaO and SiO 2 、Al 2 o 3 , FeC 2 o 4 2H 2 O pure reagents were calcined at 600°C for later use.
[0142] 102. Weigh 3g of mixed chemical reagents as shown in Table 3, put them into a platinum crucible, and hang them in a high-temperature quenching furnace with a molybdenum wire, then feed 0.8L / min high-purity argon gas, and heat up to the target temperature Keep warm for 3 hours. After the heat preservation is over, loosen the molybdenum wire and complete the water quench...
PUM
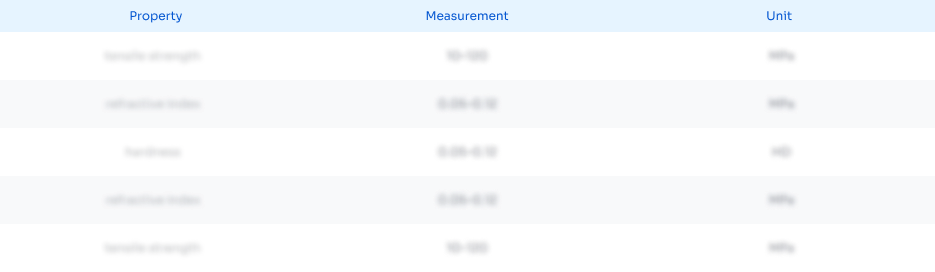
Abstract
Description
Claims
Application Information

- R&D
- Intellectual Property
- Life Sciences
- Materials
- Tech Scout
- Unparalleled Data Quality
- Higher Quality Content
- 60% Fewer Hallucinations
Browse by: Latest US Patents, China's latest patents, Technical Efficacy Thesaurus, Application Domain, Technology Topic, Popular Technical Reports.
© 2025 PatSnap. All rights reserved.Legal|Privacy policy|Modern Slavery Act Transparency Statement|Sitemap|About US| Contact US: help@patsnap.com