Ultrasonic-assisted stirring friction tunnel forming method
A friction stir, ultrasonic-assisted technology, applied in non-electric welding equipment, welding equipment, metal processing equipment, etc., can solve the problems of reducing the effective bearing area of the joint, difficulty in overflowing the forming material, reducing the strength of the product, etc., to improve the shear tension. Strength and plastic properties, solving spillage difficulties, reducing strength
- Summary
- Abstract
- Description
- Claims
- Application Information
AI Technical Summary
Problems solved by technology
Method used
Image
Examples
Embodiment Construction
[0032] In order to explain the overall concept of the present invention, the following description will be described in detail by way of example.
[0033] In the description of the invention, it is to be understood that the terms "center", "upper", "lower", "front", "post", "left", "right", "vertical", "horizontal", The orientation relationship between "top", "bottom", "inside", "outside", "axial", "radial", "circumferential", etc., based on the orientation or positional relationship shown in the drawings, only It is to facilitate the description of the present invention and simplified description, rather than indicating or implying that the device or element must have a specific orientation, and is constructed in a particular orientation, and thus is not to be construed as limiting the invention.
[0034] Moreover, the term "first", "second" is used only for the purpose of describing, and cannot be understood as an indication or implicit relative importance or implicitting the nu...
PUM
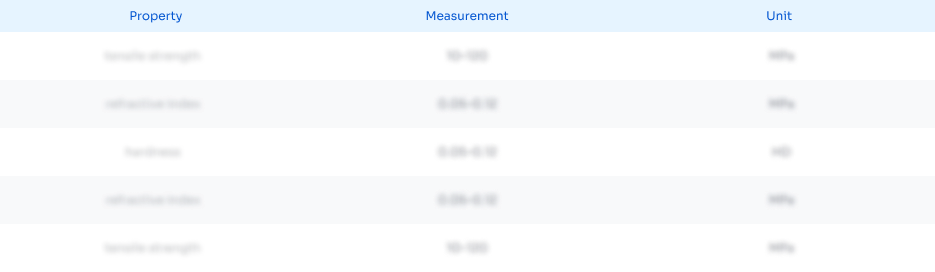
Abstract
Description
Claims
Application Information

- R&D Engineer
- R&D Manager
- IP Professional
- Industry Leading Data Capabilities
- Powerful AI technology
- Patent DNA Extraction
Browse by: Latest US Patents, China's latest patents, Technical Efficacy Thesaurus, Application Domain, Technology Topic, Popular Technical Reports.
© 2024 PatSnap. All rights reserved.Legal|Privacy policy|Modern Slavery Act Transparency Statement|Sitemap|About US| Contact US: help@patsnap.com