GMT plate and preparation method and application thereof
A sheet and composite material technology, applied in the field of GMT sheet and its preparation, can solve the problems that are not conducive to the development of lightweight GMT materials, the uniformity is not as uniform as that of the wet process, and the heating expansion height is large, so as to improve the uniformity and stability of mixing , Elasticity, Thickness Lifting Effect
- Summary
- Abstract
- Description
- Claims
- Application Information
AI Technical Summary
Problems solved by technology
Method used
Image
Examples
Embodiment 1
[0055] The GMT plate components of the present embodiment are shown in Table 1, and the preparation method may further comprise the steps:
[0056] (1) 50 parts by weight of short glass fibers with a length of 6mm and 1.0 parts by weight of vinyltrimethoxysilane coupling agent (Hangzhou Jessica Chemical Co., Ltd., KH-171) are placed at a high speed of 3000r / min. Fully mix in the mixer, the mixing time is 30min;
[0057] (2) Add 0.15 parts by weight of polyepichlorohydrin-dimethylamine-polyamine surfactant (Shaoxing Shangyu Simo Institute of Organic Chemistry, 002) and 0.10 parts by weight to the mixed solution in step (1) successively Fatty alcohol polyoxyethylene ether dispersant (Shenyang Sainio Chemical Co., Ltd., Pingpingjia 0-25), stirred in a high-speed mixer with a rotating speed of 3000r / min for 20min;
[0058] (3) Add 50 parts by weight of PP powder with a melt index of 35 and 0.10 parts by weight of fatty alcohol polyoxyethylene ether dispersant (Shenyang Sainio Che...
Embodiment 2
[0081] The GMT plate components of the present embodiment are shown in Table 1, and the preparation method may further comprise the steps:
[0082] (1) The length of 45 parts by weight is glass fiber of 9mm, vinyltriethoxysilane coupling agent (Hangzhou Jessica Chemical Co., Ltd., KH-151) of 1.3 parts by weight, at a high speed of 3200r / min Fully mix in the mixer, the mixing time is 32min;
[0083] (2) add the stearyl dimethyl benzyl ammonium chloride surfactant of 0.10 weight part successively in step (1), the double fatty acid dispersant of 0.15 weight part (Fuyang Hengli Special New Material Technology Co., Ltd. , HLT-200) was stirred in a high-speed mixer with a rotating speed of 3000r / min for 20min;
[0084] (3) Adding 55 parts by weight of PP fibers with a length of 6mm, 0.10 parts by weight of ethylene oxide condensate dispersant (Nantong Runfeng Petrochemical Co., Ltd., IW100), 0.05 parts by weight of bismuth Alkyl alcohol polyoxyethylene ether surfactant (Jinan Guoc...
Embodiment 3
[0107] The GMT plate components of the present embodiment are shown in Table 1, and the preparation method may further comprise the steps:
[0108] (1) Weigh 40 parts by weight of glass fiber with a length of 12mm and 1.5 parts by weight of vinyltriethoxysilane coupling agent (Hangzhou Jessica Chemical Co., Ltd., KH-151), at a speed of 4000r / min Fully mixed in a high-speed mixer, the silane coupling agent is used as a surface modification treatment of glass fiber to increase its hydrophilicity, which is beneficial to the subsequent mixing and molding with PP materials, and the mixing time is 35 minutes;
[0109] (2) Add 0.10 parts by weight of isomeric C10 alcohol polyoxyethylene ether (Foshan Jinjia New Material Technology Co., Ltd., 1005) surfactant, 0.20 parts by weight of fatty alcohol and ethylene oxide successively in step (1) Condensate (Nantong Runfeng Petrochemical Co., Ltd., IW100) dispersant was stirred in a high-speed mixer with a rotating speed of 4000r / min for 22...
PUM
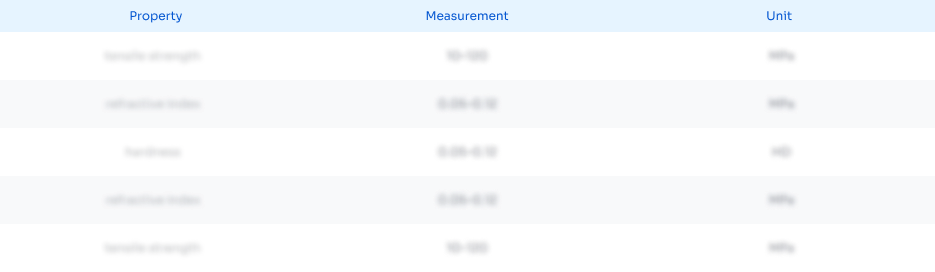
Abstract
Description
Claims
Application Information

- R&D Engineer
- R&D Manager
- IP Professional
- Industry Leading Data Capabilities
- Powerful AI technology
- Patent DNA Extraction
Browse by: Latest US Patents, China's latest patents, Technical Efficacy Thesaurus, Application Domain, Technology Topic, Popular Technical Reports.
© 2024 PatSnap. All rights reserved.Legal|Privacy policy|Modern Slavery Act Transparency Statement|Sitemap|About US| Contact US: help@patsnap.com