Preparation method of high-rate battery
A high-rate, high-power battery technology, applied in the manufacture of electrolyte batteries, lithium batteries, secondary batteries, etc., can solve problems such as voltage, and achieve the effects of simple preparation conditions, superior performance, and low production conditions
- Summary
- Abstract
- Description
- Claims
- Application Information
AI Technical Summary
Problems solved by technology
Method used
Image
Examples
preparation example Construction
[0038] Such as Figure 1-7 As shown, the specific embodiment of the present invention is a method for preparing a high-rate battery, and the specific manufacturing steps are as follows:
[0039] The first step is to prepare positive electrode slurry: weigh 90-95% positive electrode conductive material, 1.0-2.5% positive electrode binder, 1.5-4.5% positive electrode conductive agent, 0.1-3% pore regulator according to mass percentage, and weigh the above After the raw materials are added, an auxiliary solvent is added, and the mixture is mixed by a vacuum mixer to obtain a positive electrode slurry. The positive electrode binder is mainly homopolymerized or copolymerized PVDF through suspension polymerization and emulsion polymerization, and PTFE. The auxiliary solvent for the positive electrode is NMP or DMAC, etc., wherein NMP is N-methylpyrrolidone.
[0040] The second step is to prepare negative electrode slurry: weigh 90-96% negative electrode conductive material, 0.5-2....
Embodiment 1
[0060] The ratio of the number of parts of the positive electrode formula is: LCO:PVDF:SP:aluminum chloride=96:2:2:0.5
[0061] The proportion ratio of the negative electrode formula is: artificial graphite: SP: CMC: SBR: aluminum chloride = 95:1.5:1.5:2:0.5
[0062] (Because the pore regulator aluminum chloride will be removed in subsequent operations, this embodiment is calculated based on 100 parts of other substances in the positive and negative electrode formulations)
[0063] The slurry is prepared according to the well-known positive and negative electrode slurry preparation methods in the industry. Aluminum chloride can be dry-mixed with positive and negative electrode active materials, and can also be mixed with positive and negative electrode glue to make pulp. After the performance of the slurry meets the discharge conditions, it is demagnetized and pumped to the coating head for coating. The temperature of the positive electrode coating drying zone is between 60-1...
Embodiment 2
[0069] The ratio of the number of parts of the positive electrode formula is: NMC:PVDF:SP=94:2:4;
[0070] The proportion ratio of the negative electrode formula is: artificial graphite: SP: CMC: SBR: aluminum chloride = 93:3.5:1.5:2:0.5; (considering that the pore regulator aluminum chloride will be removed in subsequent operations, so this The embodiment is designed according to 100 parts of other substances of the positive and negative electrode formulations.)
[0071] The slurry is prepared according to the well-known positive and negative electrode slurry preparation methods in the industry. Aluminum chloride can be dry-mixed with the negative electrode active material, or can be mixed with the negative electrode glue and then made into pulp. After the slurry performance meets the discharge conditions, it will be demagnetized and pumped to the coating head for coating. The temperature of the positive electrode coating drying zone is between 60-120°C, and the negative ele...
PUM
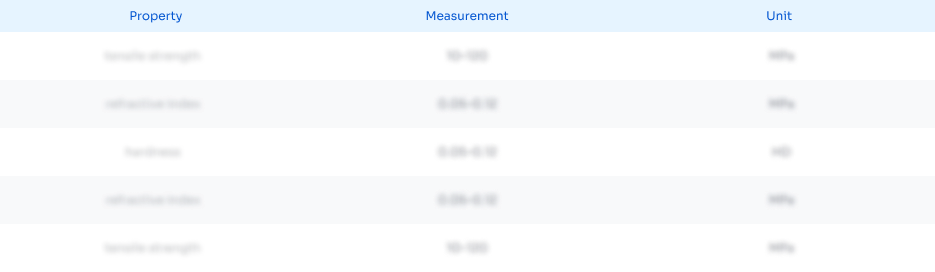
Abstract
Description
Claims
Application Information

- R&D
- Intellectual Property
- Life Sciences
- Materials
- Tech Scout
- Unparalleled Data Quality
- Higher Quality Content
- 60% Fewer Hallucinations
Browse by: Latest US Patents, China's latest patents, Technical Efficacy Thesaurus, Application Domain, Technology Topic, Popular Technical Reports.
© 2025 PatSnap. All rights reserved.Legal|Privacy policy|Modern Slavery Act Transparency Statement|Sitemap|About US| Contact US: help@patsnap.com