A milling method of gear rounding and chamfering based on geometric adaptive compensation
A technology of adaptive compensation and processing method, which is applied in the direction of belt/chain/gear, gear teeth, components with teeth, etc., which can solve the problems of heavy workload, low efficiency of manual grinding, poor consistency of manual grinding, etc.
- Summary
- Abstract
- Description
- Claims
- Application Information
AI Technical Summary
Problems solved by technology
Method used
Image
Examples
Embodiment 1
[0038] A gear rounding and chamfering milling method based on geometric self-adaptive compensation in this embodiment, the basic plan route is: complete the clamping of the gear parts under the rough reference, and combine the on-machine measurement to detect the actual clamping state of the gear parts and position, calculate the clamping error of the gear part according to the measurement data results, determine the angular position of the gear for the spiral bevel gear, adjust the machining tool path or machining coordinate system, and complete the milling of rounded or chamfered corners. The processing flow chart is as follows figure 1 Shown:
[0039] (1) Preparation before processing
[0040] The rounding and chamfering processing method of the spiral bevel gear in the present invention is a fixed contour milling process carried out under the five-axis numerical control machine tool, so relevant preparation work needs to be carried out before the machine tool is processed...
PUM
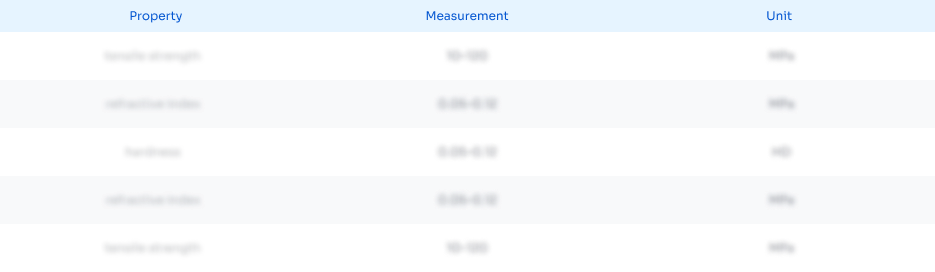
Abstract
Description
Claims
Application Information

- R&D Engineer
- R&D Manager
- IP Professional
- Industry Leading Data Capabilities
- Powerful AI technology
- Patent DNA Extraction
Browse by: Latest US Patents, China's latest patents, Technical Efficacy Thesaurus, Application Domain, Technology Topic, Popular Technical Reports.
© 2024 PatSnap. All rights reserved.Legal|Privacy policy|Modern Slavery Act Transparency Statement|Sitemap|About US| Contact US: help@patsnap.com