Process for producing chromic anhydride and ferrous oxalate by taking ferrochrome as raw material
A technology of ferrochromium alloy and ferrous oxalate, which is applied in the preparation of chromium oxide/hydrate, organic compound, chromium trioxide, etc., can solve the problems of low effective metal recovery rate, serious environmental pollution, high production cost, and improve sales. The effect of price, low mutual content and fast production speed
- Summary
- Abstract
- Description
- Claims
- Application Information
AI Technical Summary
Benefits of technology
Problems solved by technology
Method used
Examples
Embodiment 1
[0064] Accurately weigh 150g of crushed and ground ferrochrome powder, accurately measure 180ml of concentrated sulfuric acid, dilute the concentrated sulfuric acid with 360ml of water and cool to room temperature, then add all dilute sulfuric acid into the reactor, and simultaneously add 150g of ferrochrome powder It was also added into the reactor at one time, the speed of the stirrer was 200 rpm, the temperature was raised to 97°C synchronously, and the reaction was stirred at a constant temperature for 4 hours. Among them, add 700ml of evaporated water (evenly added dropwise within 4 hours), then cool down to 60°C, add water to dilute to 2100ml, stir for 20 minutes, and then filter. Obtain filter residue 22.1g, and filtrate is close to 2100ml, according to assay test result, calculate and should add industrial oxalic acid 124.97g.
[0065] Add all the filtrate 2100ml into the reactor, set the temperature at 30°C, add 124.97g of oxalic acid, stir at constant temperature for...
Embodiment 2
[0074] Accurately weigh 100g of crushed and ground ferrochrome powder, accurately measure 120ml of concentrated sulfuric acid, dilute the concentrated sulfuric acid with 240ml of water and cool to room temperature, then add all dilute sulfuric acid into the reactor, and simultaneously add 100g of ferrochrome powder It was also added into the reactor at one time, the speed of the stirrer was 200 rpm, the temperature was raised to 97.7°C synchronously, and the reaction was stirred at a constant temperature for 4 hours. Among them, add 510ml of evaporated water (evenly added dropwise within 4 hours), then cool down to 60°C, add water to dilute to 1400ml, stir for 20 minutes, and then filter. Obtain filter residue 17.8g, and filtrate is close to 1290ml, according to assay test result, calculate and should add industrial oxalic acid 111g.
[0075] Add all the filtrate 1290ml into the reactor, set the temperature at 40°C, add 111g of oxalic acid, stir at constant temperature for 30 ...
PUM
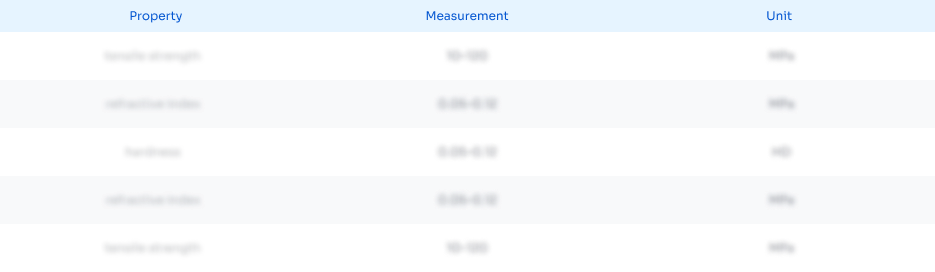
Abstract
Description
Claims
Application Information

- R&D
- Intellectual Property
- Life Sciences
- Materials
- Tech Scout
- Unparalleled Data Quality
- Higher Quality Content
- 60% Fewer Hallucinations
Browse by: Latest US Patents, China's latest patents, Technical Efficacy Thesaurus, Application Domain, Technology Topic, Popular Technical Reports.
© 2025 PatSnap. All rights reserved.Legal|Privacy policy|Modern Slavery Act Transparency Statement|Sitemap|About US| Contact US: help@patsnap.com