Permanent magnet synchronous motor vibration noise active suppression method
A permanent magnet synchronous motor, vibration and noise technology, applied in motor control, motor generator control, AC motor control and other directions, can solve the problems of cycle-by-cycle adjustment, torque ripple, zero-crossing distortion, etc., to improve data update frequency, optimized vibration and noise, easy to achieve effects
- Summary
- Abstract
- Description
- Claims
- Application Information
AI Technical Summary
Problems solved by technology
Method used
Image
Examples
Embodiment Construction
[0061] The principles and features of the present invention are described below in conjunction with the accompanying drawings, and the examples given are only used to explain the present invention, and are not intended to limit the scope of the present invention.
[0062] as attached figure 1 As shown, it is a typical architecture diagram of the three-phase permanent magnet synchronous motor system of the application object of the present invention. The whole system includes a three-phase full-bridge inverter 1, an LC filter circuit 2, a three-phase permanent magnet synchronous motor 3, and a sampling circuit 4 and control system 5, wherein the three-phase permanent magnet synchronous motor 3 is connected to the filter circuit 2 formed by LC through three power lines, and the LC filter circuit 2 is connected to the output end of the three-phase full-bridge inverter 1; the three-phase full-bridge inverter A DC support capacitor C1 is connected in series on the bus of the bridge...
PUM
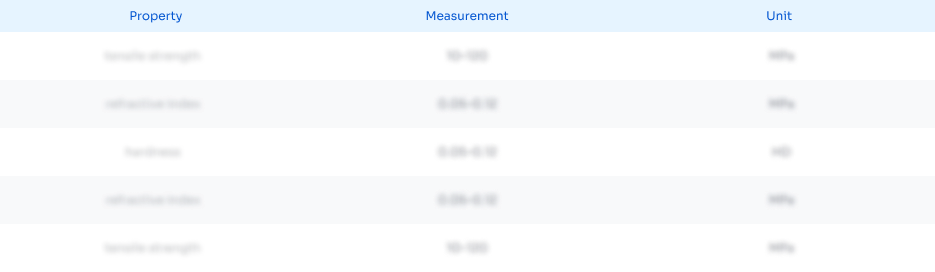
Abstract
Description
Claims
Application Information

- R&D
- Intellectual Property
- Life Sciences
- Materials
- Tech Scout
- Unparalleled Data Quality
- Higher Quality Content
- 60% Fewer Hallucinations
Browse by: Latest US Patents, China's latest patents, Technical Efficacy Thesaurus, Application Domain, Technology Topic, Popular Technical Reports.
© 2025 PatSnap. All rights reserved.Legal|Privacy policy|Modern Slavery Act Transparency Statement|Sitemap|About US| Contact US: help@patsnap.com