Low-refractive-index transparent material as well as preparation method and application thereof
A technology of transparent material and low refractive index, applied in instruments, clad optical fibers, optical components, etc., can solve the problems of complex synthesis, high optical loss, and low temperature resistance of perfluoroolefin copolymers, and achieve low refractive index, Good transparency and easy industrial preparation
- Summary
- Abstract
- Description
- Claims
- Application Information
AI Technical Summary
Problems solved by technology
Method used
Image
Examples
Embodiment 1-1
[0042] Synthesis of PDD monomer
[0043] Step (1), D456 synthesis process
[0044] Add the catalyst lithium chloride and the reaction solvent into the cyclization reactor, and replace the gas in the reactor with high-purity nitrogen; Fluoroacetone, insulation is finished to reaction, obtains D456; Its reaction equation is as follows:
[0045] Step (2), D416 synthesis procedure
[0046] Add D456 into the chlorination kettle, feed chlorine gas at a certain flow rate, close the steam valve, feed cooling water, control the temperature of the reactor to 75-85°C, and obtain D416 after chlorination is completed;
[0047] Step (3), D418 synthesis procedure
[0048] Add D416 synthesized in the chlorination process, hydrogen fluoride and catalyst antimony trifluoride into the fluorination kettle, start stirring, heat the jacket with low-pressure steam, raise the temperature to 80-90°C, and react for 3-4 hours to obtain the reaction product D418;
[0049] Step (4), PDD synthesis proc...
Embodiment 2-1
[0054] Add 2 mol of PDD monomer, 8 mol of tetrafluoroethylene (TFE), 0.08 mol of initiator diisopropyl peroxydicarbonate (that is, concentration 8‰), and fluorinated organic reaction medium trifluorotrichloroethane into the equipment for solution copolymerization, The PDD-TFE copolymer was prepared by solution copolymerization at 57°C; the molar mass ratio of PDD to tetrafluoroethylene was 20 / 80.
[0055] The PDD-TFE copolymer infrared spectrogram that embodiment 2-1 prepares is as figure 1 As shown, ~1000cm -1 for-CF 3 peaks at ~1050 and ~1150cm -1 It is a strong absorption band of C-O-C, ~1149cm -1 with 1220cm -1 for-CF 2 stretching vibration peak.
[0056] Use the perfluoroalkene ether copolymer (i.e. PDD-TFE copolymer) prepared in Example 2-1 above to prepare a transparent material:
Embodiment 3-1
[0058] After drying 48g of polymethyl methacrylate and 12g of perfluoroalkenyl ether copolymer in a vacuum oven at 80°C for 24 hours, the mass ratio of polymethyl methacrylate to perfluoroalkenyl ether copolymer is 80 / 20, After mixing and stirring at room temperature, add to the internal mixer, the temperature of the internal mixer is 230°C, the set speed is 50rpm, and the mixing time is 10min. The above kneaded samples were pressed into tablets (240° C.) by a flat vulcanizer to obtain sheets for testing light transmittance and haze.
PUM
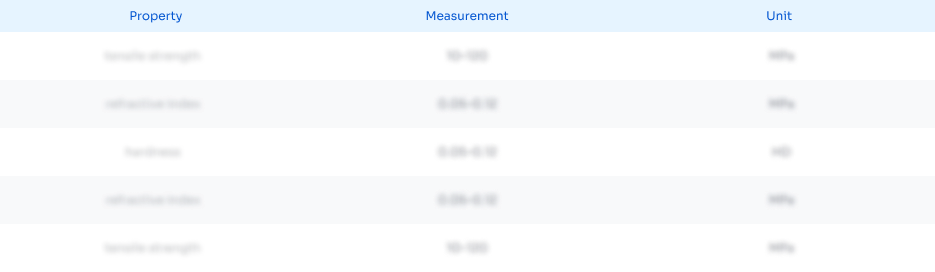
Abstract
Description
Claims
Application Information

- R&D Engineer
- R&D Manager
- IP Professional
- Industry Leading Data Capabilities
- Powerful AI technology
- Patent DNA Extraction
Browse by: Latest US Patents, China's latest patents, Technical Efficacy Thesaurus, Application Domain, Technology Topic, Popular Technical Reports.
© 2024 PatSnap. All rights reserved.Legal|Privacy policy|Modern Slavery Act Transparency Statement|Sitemap|About US| Contact US: help@patsnap.com