Glycine production process and device
A technology of production equipment and production process, which is applied in the field of chemical technology, can solve the problems of consuming large catalysts, etc., and achieve the effects of high reaction conversion rate, mild reaction conditions and less emission
- Summary
- Abstract
- Description
- Claims
- Application Information
AI Technical Summary
Problems solved by technology
Method used
Image
Examples
specific Embodiment 1
[0050] Ni / AlSiO catalyst was prepared by co-precipitation method, 50g of catalyst (Ni content 10wt%) was packed into fixed bed reactor 3, and the catalyst was reduced with hydrogen (450°C) before use. Use raw material pump 81 to send methyl glycolate into fixed bed reactor 3, use booster pump 82 to send ammonia gas into fixed bed reactor 3, methyl glycolate: ammonia = 1:6, weight hourly space velocity is 1h , when the reaction temperature was 140°C, the conversion rate was 62%, and the selectivity was 92%. The reaction product was separated by the gas-liquid separator 4 and refined by the product refining tower 6, and the product refining recovery rate was 98%.
specific Embodiment 2
[0052] Ni / AlSiO catalyst was prepared by co-precipitation method, 50g of catalyst (Ni content 10wt%) was packed into fixed bed reactor 3, and the catalyst was reduced with hydrogen (450°C) before use. Use raw material pump 81 to send methyl glycolate into fixed bed reactor 3, use booster pump 82 to send ammonia gas into fixed bed reactor 3, methyl glycolate: ammonia = 1:6, weight hourly space velocity is 1h , when the reaction temperature is 180°C, the conversion rate is 98%, the selectivity is 92%, the reaction product is separated by the gas-liquid separator 4 and refined by the product refining tower 6, and the product refining recovery rate is 98%.
specific Embodiment 3
[0054] Ni / AlSiO catalyst was prepared by co-precipitation method, 50g of catalyst (Ni content 10wt%) was packed into fixed bed reactor 3, and the catalyst was reduced with hydrogen (450°C) before use. Use raw material pump 81 to send methyl glycolate into fixed bed reactor 3, use booster pump 82 to send ammonia gas into fixed bed reactor 3, methyl glycolate: ammonia = 1:6, weight hourly space velocity is 4h When the reaction temperature is 180°C, the conversion rate is 90%, the selectivity is 98%, the reaction product is separated by the gas-liquid separator 4 and the product refining tower 6 is refined, and the product refining recovery rate is 98%.
PUM
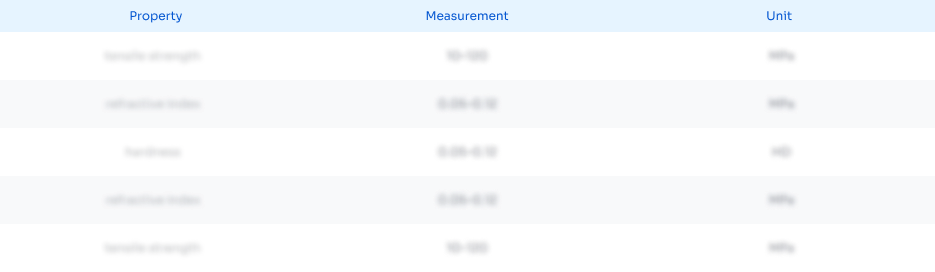
Abstract
Description
Claims
Application Information

- R&D
- Intellectual Property
- Life Sciences
- Materials
- Tech Scout
- Unparalleled Data Quality
- Higher Quality Content
- 60% Fewer Hallucinations
Browse by: Latest US Patents, China's latest patents, Technical Efficacy Thesaurus, Application Domain, Technology Topic, Popular Technical Reports.
© 2025 PatSnap. All rights reserved.Legal|Privacy policy|Modern Slavery Act Transparency Statement|Sitemap|About US| Contact US: help@patsnap.com