Mold pressing and bag pressing integrated forming process for composite chair back
A composite material and molding process technology, applied in the field of molding and bagging integrated molding process, can solve the problems of difficult bonding, time-consuming, low production efficiency, etc., so as to reduce the complexity of the material process and reduce the production cost. , the effect of stable performance
- Summary
- Abstract
- Description
- Claims
- Application Information
AI Technical Summary
Problems solved by technology
Method used
Image
Examples
Embodiment Construction
[0040] The preferred embodiments of the present invention are given below in conjunction with the accompanying drawings to describe the technical solution of the present invention in detail.
[0041] Picture 1-1 It is one of the flow charts of the integrated molding process of the composite material chair back of the present invention by molding and bagging. Figure 1-2 It is the second flow chart of the integrated molding process of molding and bagging of the composite material chair back of the present invention. Figure 1-3 It is the third flow chart of the integrated molding process of molding and bagging of the composite material chair back of the present invention. Figure 1-4 It is the fourth flow chart of the integral molding process of the composite material chair back of the present invention by molding and bagging. diagram 2-1 It is a schematic front view of the overall structure of the composite material chair back of the present invention. Figure 2-2 It is a ...
PUM
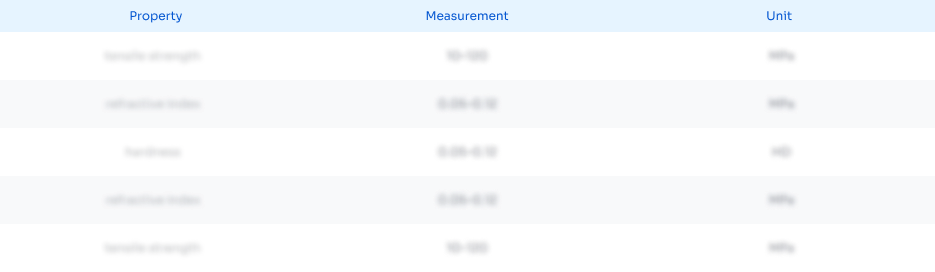
Abstract
Description
Claims
Application Information

- R&D Engineer
- R&D Manager
- IP Professional
- Industry Leading Data Capabilities
- Powerful AI technology
- Patent DNA Extraction
Browse by: Latest US Patents, China's latest patents, Technical Efficacy Thesaurus, Application Domain, Technology Topic, Popular Technical Reports.
© 2024 PatSnap. All rights reserved.Legal|Privacy policy|Modern Slavery Act Transparency Statement|Sitemap|About US| Contact US: help@patsnap.com