Anti-corrosion, anti-wear and anti-slagging device of wall type pulverized coal fired boiler
A pulverized coal boiler and anti-corrosion technology, which is applied in the field of anti-corrosion, anti-wear, and anti-slagging devices, can solve problems such as slagging, high-temperature corrosion, etc., and achieve the effects of simple system, increased oxygen content, and reduced total NOx emissions
- Summary
- Abstract
- Description
- Claims
- Application Information
AI Technical Summary
Problems solved by technology
Method used
Image
Examples
Embodiment 1
[0028] see figure 1 , is an improved schematic diagram of the corresponding pulverized coal pipelines of the burners adjacent to the two side walls in the first layer of burners. The rich-lean separation device 1 used in this embodiment is a fixed thick-lean separation device. The layers are exactly the same. When put into operation, the pulverized coal pipeline at its outlet is divided into a light phase pulverized coal pipeline 2 and a dense phase pulverized coal pipeline 3 through the separation of the fixed thick-lean separation device 1. The first burner 4 is connected with the eighth burner 11 so that its pulverized coal amount is less than the average value of the pulverized coal amount of the layer, and the dense phase pulverized coal pipeline 3 is connected with the second burner 5 and the seventh burner 10, Therefore, under the condition that the air intake of the original burner is constant, the combustion process of the pulverized coal airflow of the first burner ...
Embodiment 2
[0030] see figure 2 , this embodiment is an improved schematic diagram of the corresponding pulverized coal pipelines of the burners adjacent to the two side walls in the first layer of burners. In this embodiment, the thick-thin separation device 1 is an adjustable thick-thin separation device. The layer is exactly the same. When put into operation, the pulverized coal pipeline at the outlet is divided into a light-phase pulverized-coal pipeline 2 and a dense-phase pulverized-coal pipeline 3 through the separation function of the adjustable thick-lean separation device, and the pulverized coal pipeline can be adjusted. The light phase pulverized coal pipeline 2 is connected with the first burner 4 and the eighth burner 11 adjacent to the two side walls, so that the amount of pulverized coal is less than the average value of the pulverized coal quantity of this layer, and the pulverized coal pipeline 3 of the dense phase is connected with the second burner 11. The burner 5 i...
PUM
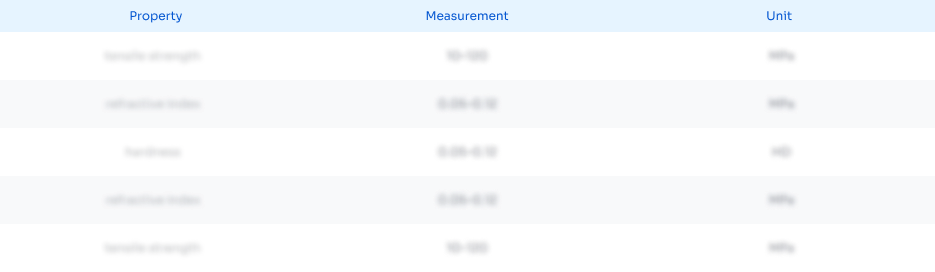
Abstract
Description
Claims
Application Information

- Generate Ideas
- Intellectual Property
- Life Sciences
- Materials
- Tech Scout
- Unparalleled Data Quality
- Higher Quality Content
- 60% Fewer Hallucinations
Browse by: Latest US Patents, China's latest patents, Technical Efficacy Thesaurus, Application Domain, Technology Topic, Popular Technical Reports.
© 2025 PatSnap. All rights reserved.Legal|Privacy policy|Modern Slavery Act Transparency Statement|Sitemap|About US| Contact US: help@patsnap.com