Forging strengthening and shaping process for nodular iron castings
A technology for ductile iron and iron castings, applied in the field of forging, can solve the problems of complex casting process control, infeasible forging process, shrinkage holes, etc., and achieve the effect of eliminating internal defects and reducing machining costs.
- Summary
- Abstract
- Description
- Claims
- Application Information
AI Technical Summary
Problems solved by technology
Method used
Examples
example 1
[0028] Step 1, the ductile iron castings are directly demolded at about 300°C after casting;
[0029] Step 2: put the ductile iron castings demolded in step 1 into the heating furnace, heat to 850°C, insert them into a closed forging die sprayed with a release agent, carry out forging strengthening and shaping with a deformation of 5%, and hold the pressure for 1.5 minutes , the release agent is a release agent containing Mg, which is made by adding magnesium powder into the boron nitride-graphite colloid release agent (graphite content≤30%), and the addition of magnesium powder in the release agent containing Mg The amount is 5%;
[0030] Step 3, after the pressure holding is completed, open the mold and take out the ductile iron casting;
[0031] Step 4, annealing the ductile iron casting.
example 2
[0033] Step 1, the ductile iron castings are directly demolded at about 300°C after casting;
[0034] Step 2: put the ductile iron castings demolded in step 1 into the heating furnace, heat to 950°C, insert them into a closed forging die sprayed with a release agent, carry out forging strengthening and shaping with a deformation of 8%, and hold the pressure for 1.5 minutes , the release agent is a release agent containing Mg, which is made by adding magnesium powder into the boron nitride-graphite colloid release agent (graphite content≤30%), and the addition of magnesium powder in the release agent containing Mg The amount is 7%;
[0035] Step 3, after the pressure holding is completed, open the mold and take out the ductile iron casting;
[0036] Step 4, annealing the ductile iron casting.
example 3
[0038] Step 1, the ductile iron castings are directly demolded at about 300°C after casting;
[0039] Step 2: put the ductile iron castings demolded in step 1 into the heating furnace, heat to 1050°C, insert them into a closed forging die sprayed with release agent, carry out forging strengthening and shaping with a deformation amount of 10%, and hold the pressure for 1.5 minutes , the release agent is a release agent containing Mg, which is made by adding magnesium powder into the boron nitride-graphite colloid release agent (graphite content≤30%), and the addition of magnesium powder in the release agent containing Mg The amount is 7%;
[0040] Step 3, after the pressure holding is completed, open the mold and take out the ductile iron casting;
[0041] Step 4, annealing the ductile iron casting.
PUM
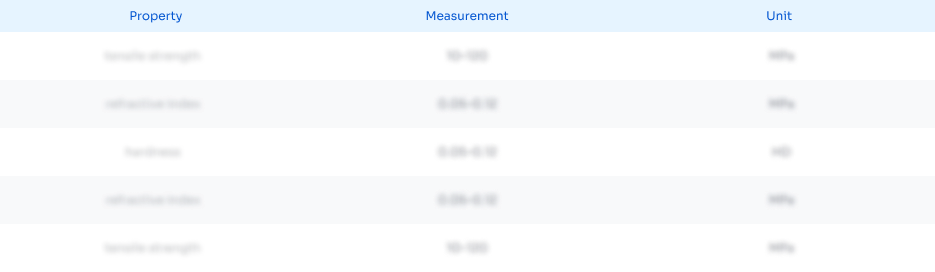
Abstract
Description
Claims
Application Information

- R&D Engineer
- R&D Manager
- IP Professional
- Industry Leading Data Capabilities
- Powerful AI technology
- Patent DNA Extraction
Browse by: Latest US Patents, China's latest patents, Technical Efficacy Thesaurus, Application Domain, Technology Topic, Popular Technical Reports.
© 2024 PatSnap. All rights reserved.Legal|Privacy policy|Modern Slavery Act Transparency Statement|Sitemap|About US| Contact US: help@patsnap.com