Scaling control method for debutanizer bottom reboiler of light hydrocarbon recovery device
A technology for recovery of debutanizer and light hydrocarbons, which is applied in chemical instruments and methods, separation methods, distillation adjustment/control, etc. Reduced reboiler heat transfer efficiency, limited reboiler steam flow, etc., to reduce reboiler scaling, slow down scaling rate, and improve scaling effects
- Summary
- Abstract
- Description
- Claims
- Application Information
AI Technical Summary
Problems solved by technology
Method used
Image
Examples
Embodiment 1
[0033] During the operation of the light hydrocarbon recovery unit, the antiscalant is injected into the feed section of the debutanizer, specifically before the feed pump, to facilitate the mixing of the antiscalant and naphtha. The injection amount of the antiscalant is 25-35mg / kg (based on the amount of feed to the debutanizer), that is, inject 25-35 mg of scale inhibitor per kg of feed, and the scale inhibitor used is Baker Hughes scale inhibitor BPR372133. Antiscalants are stored in buffer tanks under nitrogen blanketing.
[0034] According to the above method, two sets of identical light hydrocarbon recovery devices were tested.
[0035] The following are two sets of equipment 1# device and 2# device used by the applicant himself, using the experimental data after the application method.
[0036] Data selection based on:
[0037] (1) The debutanizer of the 2# unit has been overhauled twice, and the comparison is obvious;
[0038] (2) During the maintenance of 1# unit...
Embodiment 2
[0083] Use the method of Example 1 to inject the scale inhibitor. At the same time, inject the corrosion inhibitor at the top of the debutanizer. The minimum flow rate needs to be mixed evenly with the liquefied gas first, and then injected into the debutanization gas phase volatilization line. The amount of corrosion inhibitor used is 3-8mg / kg (based on the top liquefied gas flow rate of the debutanizer). Corrosion inhibitors are stored in buffer tanks under nitrogen blanketing.
[0084] On December 23, 2019, the corrosion inhibitor was injected into the top of the 2# debutanizer tower. By tracking and observing the feed buffer tank V0101 of the debutanizer tower and the iron ion content of the debutanizer reflux tank V0102, it was found that the injection of the corrosion inhibitor The content of iron ions in the water bag (as shown in the figure below) has dropped significantly (such as Figure 12 , Figure 13 shown).
[0085] By injecting the corrosion inhibitor and obs...
Embodiment 3
[0092] Generally, in order to reduce steam transmission loss in public workshops, supersaturated steam is usually used for transmission. However, due to the high degree of superheat of the steam entering the device at 3.6MPa, the steam needs to be cooled to the saturation temperature after entering the reboiler. During this period of time, the energy released by the steam is small and the temperature is relatively high. The rate is slower than that of the phase transition, so that the upper tube bundle of the reboiler maintains a high temperature for a period of time, forming a high temperature section. Increase the probability of high temperature polymerization of olefins at the tube bundle. Add a temperature and pressure reducer to the 3.6MPa heat source steam pipeline at the bottom of the debutanizer, and inject medium-pressure deoxygenated water to reduce the temperature of the steam at the bottom of the tower from 360°C to 280°C, and reduce the temperature of the steam in...
PUM
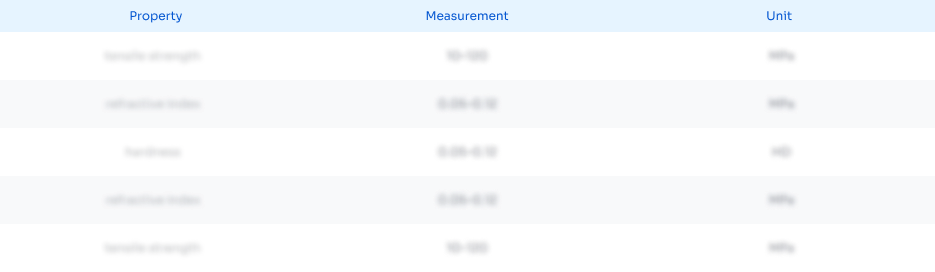
Abstract
Description
Claims
Application Information

- R&D
- Intellectual Property
- Life Sciences
- Materials
- Tech Scout
- Unparalleled Data Quality
- Higher Quality Content
- 60% Fewer Hallucinations
Browse by: Latest US Patents, China's latest patents, Technical Efficacy Thesaurus, Application Domain, Technology Topic, Popular Technical Reports.
© 2025 PatSnap. All rights reserved.Legal|Privacy policy|Modern Slavery Act Transparency Statement|Sitemap|About US| Contact US: help@patsnap.com