Preparation method of bipolar membrane
A technology of bipolar membranes and basement membranes, applied in chemical instruments and methods, membranes, membrane technologies, etc., can solve unfavorable ion rapid exchange and transfer, low degree of dissociation of sodium carboxylate groups, slow ion exchange speed, etc. problem, to achieve the effect of accelerating water dissociation, improving water dissociation efficiency, and improving ion exchange capacity
- Summary
- Abstract
- Description
- Claims
- Application Information
AI Technical Summary
Problems solved by technology
Method used
Image
Examples
Embodiment 1
[0026] In the embodiment of the present invention, a method for preparing a bipolar membrane is disclosed, which specifically includes the following steps:
[0027] S1. Mix 30% polypropylene, 5% ethylene propylene copolymer, 60% ethylene butene copolymer, and 5% ethylene octene copolymer evenly, heat to 200-230°C for kneading and granulation, after drying, flow Extended into a raw material film with a thickness of 0.2mm;
[0028] S2. Mix 55% absolute ethanol, 40% styrene monomer, and 5% divinylbenzene monomer to form an irradiation solution, place it in a stainless steel bucket, and cut the raw material film prepared in step S1 to the required size (determined according to actual production requirements), then immerse the cut raw material film in the irradiation liquid, seal the stainless steel barrel, feed nitrogen, and place it in a constant temperature box at 5°C, and use 60Coγ-rays to irradiate and graft at a constant temperature , the irradiation dose is 5KGy, after irra...
Embodiment 2
[0034] S1. Mix 35% polypropylene and 65% ethylene-butylene copolymer evenly, heat to 150-230°C for kneading and granulation, after drying, cast to make a raw material film with a thickness of 0.23mm;
[0035] S2. Mix 50% absolute ethanol, 38% styrene monomer, and 12% divinylbenzene monomer to form an irradiation solution, place it in a stainless steel barrel, and cut the raw material film prepared in step S1 to the required size (determined according to actual production requirements), and then immerse the cut raw material film in the irradiation liquid, seal the stainless steel barrel, feed nitrogen, and place it in a constant temperature box at 0°C, and use 60Coγ-rays to irradiate and graft at a constant temperature , the irradiation dose is 4.5KGy, after irradiation and grafting, use polyethylene glycol aqueous solution to soak for 24 hours, and after drying, the basement membrane for preparing the ion exchange membrane is obtained;
[0036] S3. Introduce anion / cation excha...
Embodiment 3
[0041] S1. Mix 30% polypropylene, 65% ethylene-butylene copolymer, and 5% ethylene-octene copolymer evenly, heat to 180-230°C for kneading and granulation, and after drying, cast to make a 0.25mm thick Raw film;
[0042] S2. Mix 60% absolute ethanol, 25% styrene monomer, and 15% divinylbenzene monomer to form an irradiation solution, place it in a stainless steel barrel, and cut the raw material film prepared in step S1 to the required size (determined according to actual production requirements), and then immerse the cut raw material film in the irradiation liquid, seal the stainless steel barrel, feed nitrogen, and place it in a constant temperature box at 0°C, and use 60Coγ-rays to irradiate and graft at a constant temperature , the irradiation dose is 5KGy, after irradiation and grafting, use polyethylene glycol aqueous solution to soak for 18 hours, and after drying, obtain the basement membrane for preparing ion-exchange membrane;
[0043] S3. Introduce anion / cation exc...
PUM
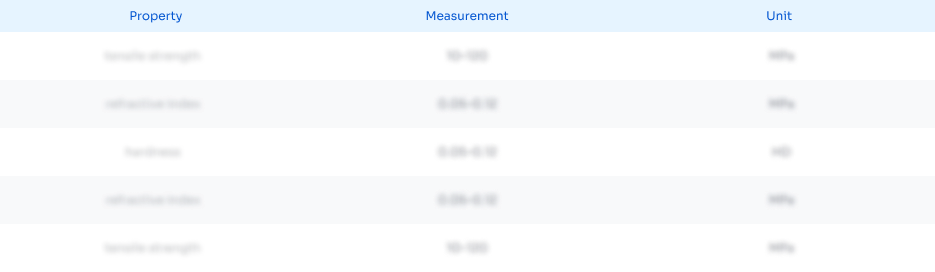
Abstract
Description
Claims
Application Information

- R&D Engineer
- R&D Manager
- IP Professional
- Industry Leading Data Capabilities
- Powerful AI technology
- Patent DNA Extraction
Browse by: Latest US Patents, China's latest patents, Technical Efficacy Thesaurus, Application Domain, Technology Topic, Popular Technical Reports.
© 2024 PatSnap. All rights reserved.Legal|Privacy policy|Modern Slavery Act Transparency Statement|Sitemap|About US| Contact US: help@patsnap.com