Cathode electrophoretic paint with environment-friendly pretreatment and high matching property and preparation method thereof
A cathodic electrophoretic coating and electrophoretic coating technology, applied in electrophoretic coatings, coatings, etc., can solve problems such as poor salt spray resistance, low throwing power, and paint film defects, so as to improve wet adhesion and wet film resistance Effect
- Summary
- Abstract
- Description
- Claims
- Application Information
AI Technical Summary
Problems solved by technology
Method used
Image
Examples
Embodiment 1
[0026] The preparation of embodiment 1 phenolic resin modified epoxy resin
[0027]
[0028] * Prepared by the reaction of diethylenetriamine and methyl isobutyl ketone in a molar ratio of 1:2, the solid content of the final product is: 73%
[0029] In the reaction flask equipped with a thermometer, a stirrer and a reflux condenser, sequentially add the E51 epoxy resin, bisphenol A type phenolic resin, bisphenol A and the first part of methyl isobutyl ketone in the formula amount. After the feeding is complete, start stirring and heat the reaction system to 150° C. and keep it warm. After adding dimethylbenzylamine, the temperature is raised to 150° C., and continue to react for 2 hours at this temperature. When the epoxy equivalent of the reaction system reaches the theoretical value ( EEW=1500), start to lower the temperature; when the system temperature drops below 100°C, add N-methylethanolamine and ketimine, the second part of methyl isobutyl ketone into the reaction s...
Embodiment 2
[0030] The preparation of embodiment 2 polyether phosphate
[0031]
[0032] Add polyphosphoric acid and polyether polyol sequentially into a reaction flask equipped with a thermometer, a stirrer and a reflux condenser, heat up to 80°C, and stir for 5 hours. After cooling down to room temperature, add 5 times more water to the four-neck flask, then add the phosphate ester made before, raise the temperature to 80°C, stir for 4 hours, and then cool down to room temperature. Then add ethyl acetate, after fully shaking, pour into the separatory funnel to stand for stratification, pour off the lower part of the water, then add saturated saline, shake fully, then let stand to separate the lower layer of water, and then add anhydrous sodium sulfate Dry until the solution becomes clear, filter out sodium sulfate, and finally use a rotary evaporator to remove the solvent by rotary evaporation to obtain polyether phosphate.
[0033]
[0034]
[0035] * Prepared by the reaction...
Embodiment 3
[0037] The preparation of embodiment 3 curing agent
[0038]
[0039] Add the formulated amount of 4,4`-diphenylmethane diisocyanate and dibutyltin dilaurate into the reaction flask equipped with a thermometer, stirrer and reflux condenser, stir and heat up to 60°C and start to add ethylene glycol mono For butyl ether, cool down with a water bath during the dropwise addition and control the temperature not to exceed 65°C. After the dropwise addition, continue to react at 80°C for 2 hours, and use the standard di-n-butylamine back titration method to analyze the remaining isocyanate group content in the reaction system. When the remaining isocyanate content is less than 0.2%, methyl isobutyl ketone is added for dilution to obtain a fully blocked isocyanate crosslinking agent with a final solid content of 80%.
PUM
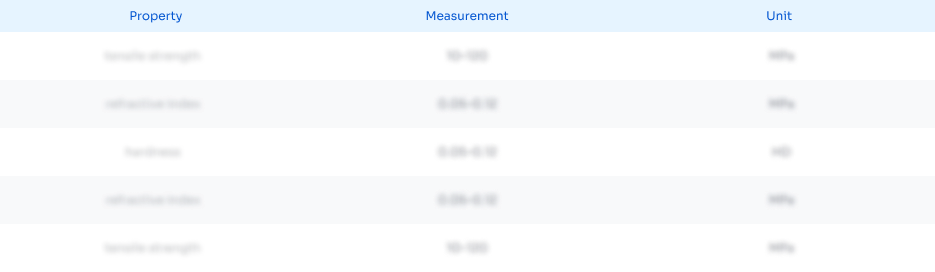
Abstract
Description
Claims
Application Information

- R&D
- Intellectual Property
- Life Sciences
- Materials
- Tech Scout
- Unparalleled Data Quality
- Higher Quality Content
- 60% Fewer Hallucinations
Browse by: Latest US Patents, China's latest patents, Technical Efficacy Thesaurus, Application Domain, Technology Topic, Popular Technical Reports.
© 2025 PatSnap. All rights reserved.Legal|Privacy policy|Modern Slavery Act Transparency Statement|Sitemap|About US| Contact US: help@patsnap.com