Preparation method of high-purity polyferric chloride
A polymeric ferric chloride, high-purity technology, applied in chemical instruments and methods, ferric halide, water/sewage treatment, etc., can solve the problems of lack of feeding mechanism, affect equipment operation, and reduce the efficiency of stirring, etc., to increase contact The effect of increasing the area, improving the stirring efficiency, and increasing the utilization rate
- Summary
- Abstract
- Description
- Claims
- Application Information
AI Technical Summary
Problems solved by technology
Method used
Image
Examples
Embodiment 1
[0040] A preparation method of high-purity polyferric chloride, the high-purity polyferric chloride comprises the following raw materials in parts by weight: 100 parts of coal gangue, 50 parts of sulfuric acid, 70 parts of hydrochloric acid, 3 parts of polymerization agent and 3 parts of oxidant;
[0041] The preparation method of this high-purity polyferric chloride comprises the steps:
[0042] S1, pulverization: put the coal gangue into a pulverizer to pulverize, and pass through a 250-mesh sieve to obtain coal gangue powder;
[0043] S2. Roasting: Put the coal gangue powder into a muffle furnace, and roast at a temperature of 700°C for 1 hour;
[0044] S3. Acid leaching: mix the roasted coal gangue powder with sulfuric acid, add hydrochloric acid to carry out acid dissolution reaction at a temperature of 90° C., and the reaction time is 2 hours. After the reaction, filter the reaction solution to obtain a pickling solution;
[0045] S4. Oxidation: Mix the pickling solutio...
Embodiment 2
[0048] A preparation method of high-purity polyferric chloride, the high-purity polyferric chloride comprises the following raw materials in parts by weight: 110 parts of coal gangue, 55 parts of sulfuric acid, 75 parts of hydrochloric acid, 4 parts of polymerization agent and 4 parts of oxidant;
[0049] The preparation method of this high-purity polyferric chloride comprises the steps:
[0050] S1, pulverization: put the coal gangue into a pulverizer to pulverize, and pass through a 250-mesh sieve to obtain coal gangue powder;
[0051] S2. Roasting: put the coal gangue powder into a muffle furnace, and roast at a temperature of 750°C for 1.5 hours;
[0052] S3. Acid leaching: mix the roasted coal gangue powder with sulfuric acid, add hydrochloric acid to carry out acid dissolution reaction at a temperature of 100° C., and the reaction time is 2.5 hours. After the reaction, the reaction solution is filtered to obtain a pickling solution;
[0053] S4. Oxidation: Mix the pickl...
Embodiment 3
[0056] A preparation method of high-purity polyferric chloride, the high-purity polyferric chloride comprises the following raw materials in parts by weight: 120 parts of coal gangue, 60 parts of sulfuric acid, 80 parts of hydrochloric acid, 5 parts of polymerization agent and 5 parts of oxidant;
[0057] The preparation method of this high-purity polyferric chloride comprises the steps:
[0058] S1, pulverization: put the coal gangue into a pulverizer to pulverize, and pass through a 250-mesh sieve to obtain coal gangue powder;
[0059] S2. Roasting: Put the coal gangue powder into a muffle furnace, and roast at a temperature of 800°C for 2 hours;
[0060] S3. Acid leaching: mix the roasted coal gangue powder with sulfuric acid, add hydrochloric acid to carry out acid dissolution reaction at a temperature of 110° C., and the reaction time is 3 hours. After the reaction, the reaction solution is filtered to obtain a pickling solution;
[0061] S4. Oxidation: Mix the pickling ...
PUM
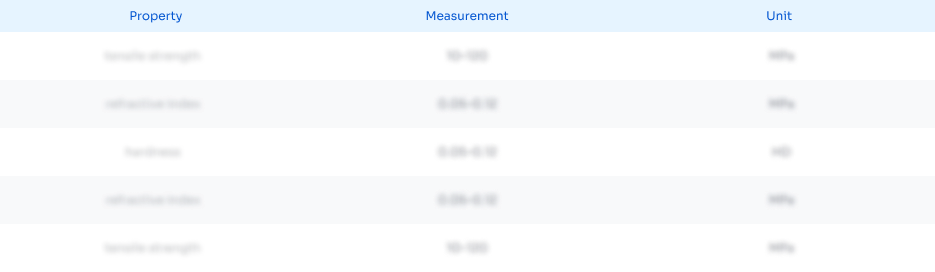
Abstract
Description
Claims
Application Information

- R&D Engineer
- R&D Manager
- IP Professional
- Industry Leading Data Capabilities
- Powerful AI technology
- Patent DNA Extraction
Browse by: Latest US Patents, China's latest patents, Technical Efficacy Thesaurus, Application Domain, Technology Topic, Popular Technical Reports.
© 2024 PatSnap. All rights reserved.Legal|Privacy policy|Modern Slavery Act Transparency Statement|Sitemap|About US| Contact US: help@patsnap.com