Pre-welding sectional type heating and press-fitting method and device
A segmented, press-fitting technology, applied in welding equipment, metal processing, laser welding equipment, etc., can solve the problems that the laser welding effect cannot be effectively guaranteed, the efficiency of piston processing is affected, and the oxide layer is prone to appear on the bonding surface. Achieve the effects of controllable press-fit interference, ensure press-fit quality, and shorten heating time
- Summary
- Abstract
- Description
- Claims
- Application Information
AI Technical Summary
Problems solved by technology
Method used
Image
Examples
Embodiment 1
[0056] Such as figure 1 As shown, a method of segmented heating and press-fitting before welding of the present invention is used for heating and press-fitting of the inner ring and outer ring interference fit of the steel piston of an automobile engine and includes the following steps:
[0057] S1. The inner ring and outer ring of the steel piston move to the induction heating station before press-fitting. There are multiple induction heating stations. Uniformity of temperature, reducing temperature difference;
[0058] S2. Move the heated inner ring and outer ring to the press-fitting station, and press-fit into a steel piston;
[0059] S3. The press-fitted steel piston is moved to the pre-heating station before welding, and the steel piston is heated as a whole to the temperature required for welding.
[0060] In step S1, the temperature difference between the inner ring and the outer ring after heating is less than or equal to 50°C, that is, the temperature of the outer ...
Embodiment 2
[0084] A method of segmented heating and press-fitting before welding of the present invention comprises the following steps:
[0085] S1. The inner ring and outer ring of the steel piston move to the induction heating station before press-fitting. There are multiple induction heating stations. The uniformity of temperature reduces the temperature difference; the inner ring and outer ring are heated to 290°C and 310°C respectively, and then the heat preservation state is automatically turned on until the induction heating ends before pressing;
[0086] S2. Move the heated inner ring and outer ring to the press-fitting station, and press-fit into a steel piston;
[0087] S3. The press-fitted steel piston is moved to the pre-welding preheating station, and the steel piston is heated as a whole to the temperature required for welding; and then the welding seam of the inner ring and the outer ring is laser welded.
[0088]During the heating process in step S1, the temperature of ...
Embodiment 3
[0111] The difference between this embodiment and embodiment 2 is:
[0112] The steel piston is welded directly after press-fitting, and the press-fitting process of step S2 is completed in 15 seconds. The temperature of the press-fitted steel piston is still 270°C, so laser welding can be performed directly, which reduces the heating process before press-fitting and reduces the overall Power consumption, simplifies the structure of the machined steel piston device.
[0113] All the other contents are identical with embodiment 2.
PUM
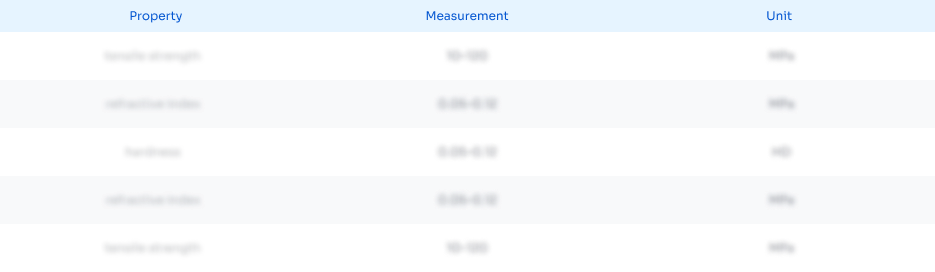
Abstract
Description
Claims
Application Information

- R&D
- Intellectual Property
- Life Sciences
- Materials
- Tech Scout
- Unparalleled Data Quality
- Higher Quality Content
- 60% Fewer Hallucinations
Browse by: Latest US Patents, China's latest patents, Technical Efficacy Thesaurus, Application Domain, Technology Topic, Popular Technical Reports.
© 2025 PatSnap. All rights reserved.Legal|Privacy policy|Modern Slavery Act Transparency Statement|Sitemap|About US| Contact US: help@patsnap.com