Preparation method and application of M-N-C monatomic catalyst
A catalyst and atomic technology, applied in the field of preparation of M-N-C single-atom catalysts, can solve the problems of difficult to clarify the structure-activity relationship between precursors and product catalysts, the catalyst sites are not necessarily uniform, and cannot be utilized, etc. Easy, low-cost, easy-to-remove effect
- Summary
- Abstract
- Description
- Claims
- Application Information
AI Technical Summary
Problems solved by technology
Method used
Image
Examples
Embodiment 1
[0041] Take 2g of copper oxide and 1g of glycoluril into the ball mill jar, and mill for 2 hours. Transfer the resulting powder to a tube furnace at 5% H 2 / N 2 In the atmosphere, heat to 250°C at 5°C / min and keep it for 4 hours, then switch the atmosphere to N 2 And heated at 5°C / min to 900°C and kept for 3 hours. After the tube furnace was naturally cooled to room temperature, the product was taken out and put into 6mol L -1 Washed in hydrochloric acid for 120 hours. Afterwards, it was suction-filtered and washed with deionized water until neutral, and the filter cake was put into an oven at 60°C for 24 hours to obtain a Cu-N-C-1 single-atom catalyst. According to X-ray photoelectron spectroscopy (XPS), the content of metal elements in the catalyst is 2.3wt.%, and the content of nitrogen elements is 9.5wt.%.
Embodiment 2
[0046] Example 2: Take 2g of copper oxide and 0.8g of glycoluril into a ball mill jar, and ball mill for 2 hours. Transfer the resulting powder to a tube furnace at 5% H 2 / N 2 In the atmosphere, heat to 250°C at 5°C / min and keep it for 4 hours, then switch the atmosphere to N 2 And heated at 5°C / min to 900°C and kept for 3 hours. After the tube furnace was naturally cooled to room temperature, the product was taken out and put into 6mol L -1 Washed in hydrochloric acid for 120 hours. Afterwards, it was suction-filtered and washed with deionized water until neutral, and the filter cake was put into an oven at 60°C for 24 hours to obtain a Cu-N-C-0.8 single-atom catalyst.
Embodiment 3
[0047] Example 3: Take 2g of copper oxide and 1.25g of glycoluril into a ball mill jar, and ball mill for 2 hours. Transfer the resulting powder to a tube furnace at 5% H 2 / N 2 In the atmosphere, heat to 250°C at 5°C / min and keep it for 4 hours, then switch the atmosphere to N 2 And heated at 5°C / min to 900°C and kept for 3 hours. After the tube furnace was naturally cooled to room temperature, the product was taken out and put into 6mol L -1 Washed in hydrochloric acid for 120 hours. Afterwards, it was suction-filtered and washed with deionized water until neutral, and the filter cake was put into an oven at 60°C for 24 hours to obtain a Cu-N-C-1.25 single-atom catalyst.
PUM
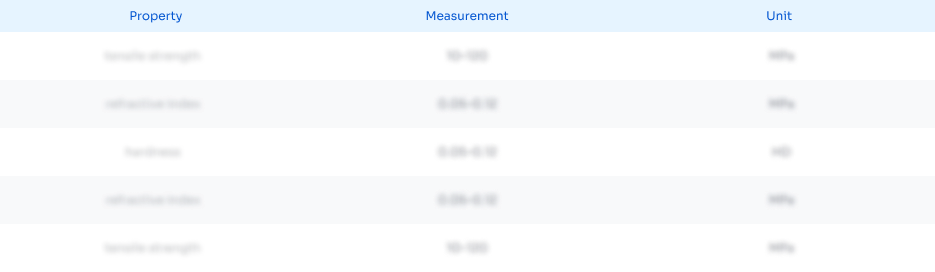
Abstract
Description
Claims
Application Information

- R&D Engineer
- R&D Manager
- IP Professional
- Industry Leading Data Capabilities
- Powerful AI technology
- Patent DNA Extraction
Browse by: Latest US Patents, China's latest patents, Technical Efficacy Thesaurus, Application Domain, Technology Topic, Popular Technical Reports.
© 2024 PatSnap. All rights reserved.Legal|Privacy policy|Modern Slavery Act Transparency Statement|Sitemap|About US| Contact US: help@patsnap.com