Method and system for machining micro-nano structure with array anti-reflection function
A technology of micro-nano structure and processing method, which is applied in the direction of metal processing equipment, manufacturing tools, welding equipment, etc., can solve the problems of low efficiency, poor precision and consistency, and achieve the goal of improving preparation efficiency, improving manufacturing efficiency, and flexible manufacturing means Effect
- Summary
- Abstract
- Description
- Claims
- Application Information
AI Technical Summary
Problems solved by technology
Method used
Image
Examples
Embodiment 1
[0081] The system composition used in this embodiment is as follows: figure 1 As shown, it is composed of laser, SLM spatial light modulator, scanning galvanometer, field mirror and coaxial observation CCD and other components. In other embodiments, the field lens can also be replaced by a microscope objective lens.
[0082] The output laser light of the laser enters the SLM spatial light modulator, and the SLM spatial light modulator divides the laser beam into array processing beams, which are reflected to the field mirror by the scanning galvanometer, and the array processing beams are focused to the working surface by the field mirror, realizing the array micro nanostructure processing.
[0083] The specific method is realized through the following steps:
[0084] (1) Carry out process tests to determine the adjustable range h of each micro-nano structure. The micro-nano structure can be a blind hole on the surface of the workpiece, and the radial section of the hole ca...
Embodiment 2
[0112] The system adopted in this embodiment adds a Fesnel lens on the basis of the embodiment, and the laser is shaped into an array Bessel processing beam through the SLM spatial light modulator, and the array Bessel processing beam is realized by superimposing the Fesnel lens. Not at the same position (realize three-dimensional shaping of laser space), the working surface of the beam is directly shaped into a shape distributed along the surface shape of the component. Compared with the first embodiment, the processing process does not need to consider the manufacturing adjustable range h. like Figure 8 shown.
[0113] The specific method is realized through the following steps:
[0114] (1) Divide the surface part to be processed into several sub-regions:
[0115] like Figure 8 In b, based on the requirement that the scanning galvanometer can scan the maximum range D at one time, the curved surface part is divided into several sub-areas, and the maximum side length L o...
PUM
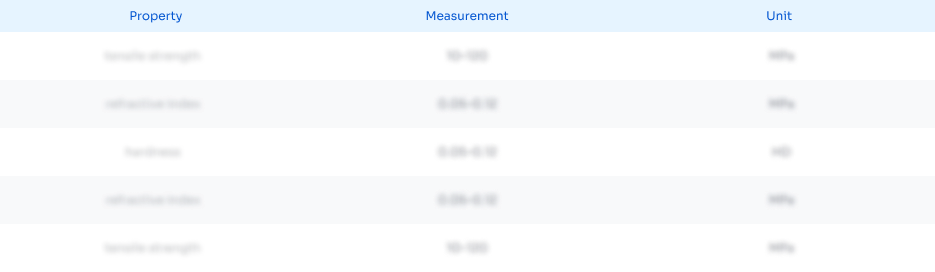
Abstract
Description
Claims
Application Information

- Generate Ideas
- Intellectual Property
- Life Sciences
- Materials
- Tech Scout
- Unparalleled Data Quality
- Higher Quality Content
- 60% Fewer Hallucinations
Browse by: Latest US Patents, China's latest patents, Technical Efficacy Thesaurus, Application Domain, Technology Topic, Popular Technical Reports.
© 2025 PatSnap. All rights reserved.Legal|Privacy policy|Modern Slavery Act Transparency Statement|Sitemap|About US| Contact US: help@patsnap.com