Precision forging near-net forming technology for light alloy non-revolving body special-shaped integral pull rod
A non-revolving, near-net-shape technology, used in railway car body parts, metal processing equipment, forging/pressing/hammer devices, etc. brittleness etc.
- Summary
- Abstract
- Description
- Claims
- Application Information
AI Technical Summary
Problems solved by technology
Method used
Image
Examples
specific Embodiment
[0058] A: Aluminum alloy non-rotating special-shaped integral tie rod technology implementation method:
[0059] Step 1: Design the dimensions and specifications of the thick-walled pipe material 1' to be forged according to the drawings, such as Figure 8 .
[0060] Step 2: Use the radial precision forging machine 3, and use the forging hammer head 2 to complete the forging and elongation of the tie rod parts, such as Figure 9 .
[0061] Step 3: After the forging and drawing are completed, replace the forging hammer head 2, and then use the radial precision forging machine 3 to forge and reduce the diameter of the tie rod end 12', such as Figure 10 .
[0062] Step 4: After the forging diameter reduction is completed, replace the forging hammer head 2, and then use the radial precision forging machine 3 to forge and flatten the end 12' of the tie rod, as shown in Figure 11 .
[0063] Step 5: Forging is completed, and the end 12' of the tie rod is machined to form a fi...
PUM
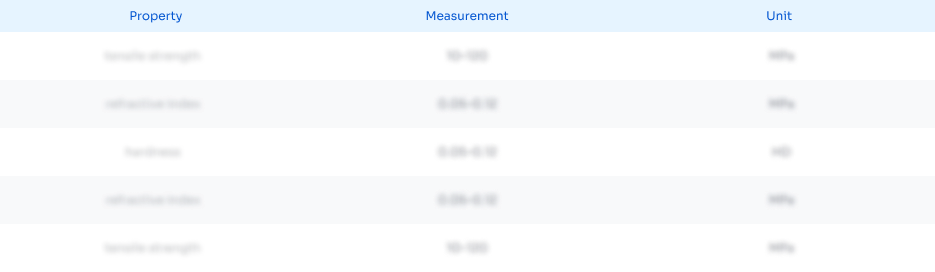
Abstract
Description
Claims
Application Information

- R&D
- Intellectual Property
- Life Sciences
- Materials
- Tech Scout
- Unparalleled Data Quality
- Higher Quality Content
- 60% Fewer Hallucinations
Browse by: Latest US Patents, China's latest patents, Technical Efficacy Thesaurus, Application Domain, Technology Topic, Popular Technical Reports.
© 2025 PatSnap. All rights reserved.Legal|Privacy policy|Modern Slavery Act Transparency Statement|Sitemap|About US| Contact US: help@patsnap.com