Heat treatment process oil gas recovery device and method
A technology of heat treatment process and recovery device, which is applied in the field of metal processing, can solve problems such as large power consumption, heat loss, air pollution, etc., and achieve the effects of reducing oil and gas emissions, slowing down high-temperature oxidation, and realizing recycling
- Summary
- Abstract
- Description
- Claims
- Application Information
AI Technical Summary
Problems solved by technology
Method used
Image
Examples
Embodiment 1
[0030] Such as figure 2 As shown, in a heat treatment furnace 1, put 25 tons of aluminum foil at a time, but connect the exhaust pipe and intake pipe of the heat treatment furnace to the system described in the manual, and open the valve at the inert gas inlet 3, so that the deep The cooler is filled with inert gas, the second fan 10 is turned on, the second three-way valve 8 is opened, the exhaust pipe 12 is communicated with the atmosphere, the first fan 6 is turned on, the inert gas enters the heat treatment furnace 1, and the air is discharged from the second After the second three-way valve 8 is extruded, the second three-way valve 8 is adjusted to be connected to the exhaust pipe 12, and the gas enters the heat exchanger group, so that the inert gas continues to circulate with the operation of the fan, and the inert gas inlet 3 is closed. The valve at the cryocooler 2 sprays liquid inert gas, heat treatment, heating and heat preservation according to the process establi...
Embodiment 2
[0034] Such as image 3 As shown, the exhaust pipes and intake pipes of the two heat treatment furnaces are connected to the system of the present invention. The two heat treatment furnaces can produce synchronously or in staggered steps, and can be adjusted by valves without interfering with each other.
[0035] The working process of the two heat treatment furnaces opens the valve at the inert gas inlet 3, makes the cryocooler 2 full of gas carbon dioxide, turns on the second fan 10, turns on the second fan 10, opens the second three-way valve 8, and makes the exhaust The trachea 12 communicates with the atmosphere, and the first blower 6 is turned on so that the carbon dioxide enters the heat treatment furnace 1 and the air is extruded from the second three-way valve 8, and the second adjusted gas is connected to the sub-exhaust pipeline 12, and after the general exhaust The gas pipe 11 enters the heat exchanger group, so that the carbon dioxide gas is continuously circulat...
Embodiment 3
[0039] Such as figure 1 As shown, the exhaust pipes and intake pipes of n heat treatment furnaces (n≥3) are connected to the system of the present invention, and the n heat treatment furnaces can be produced synchronously or in staggered steps. Through valve adjustment, Do not interfere with each other.
[0040] The treatment process of each is the same as in Example 1. When one of the heat treatment furnaces has completed a batch of aluminum foil heat treatment, the oil and gas have been completely discharged during the cooling process, and the first tee corresponding to the completed heat treatment furnace 1 should be adjusted. The valve 7 and the second three-way valve 8 connect the gas in and out of the heat treatment to the atmosphere, which avoids the waste of inert gases such as liquid carbon dioxide or liquid nitrogen, and does not affect the normal production of other furnaces. At the same time, it avoids opening the furnace door to extract aluminum foil. Asphyxiatio...
PUM
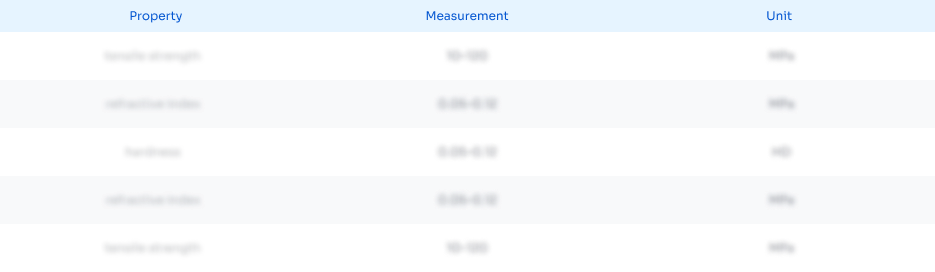
Abstract
Description
Claims
Application Information

- R&D
- Intellectual Property
- Life Sciences
- Materials
- Tech Scout
- Unparalleled Data Quality
- Higher Quality Content
- 60% Fewer Hallucinations
Browse by: Latest US Patents, China's latest patents, Technical Efficacy Thesaurus, Application Domain, Technology Topic, Popular Technical Reports.
© 2025 PatSnap. All rights reserved.Legal|Privacy policy|Modern Slavery Act Transparency Statement|Sitemap|About US| Contact US: help@patsnap.com