Magnetohydrodynamic linear vibration sensor with runway type structure
A technology of magnetohydrodynamics and linear vibration, applied in instruments, electromagnetic means, measuring devices, etc., can solve the problems of large temperature influence, narrow bandwidth, high noise, etc., and achieve stable structure, low power consumption, and low noise. Effect
- Summary
- Abstract
- Description
- Claims
- Application Information
AI Technical Summary
Problems solved by technology
Method used
Image
Examples
Embodiment Construction
[0026] In this embodiment, a magnetohydrodynamic linear vibration sensor includes a shape design of the sensor such as image 3 shown, and the magnetic circuit design inside the case, such as figure 1 , figure 2 As shown, its metal shell is composed of a base 3 and an end cover 1, and a groove 2 is formed inside the base 3 for fixing various components in contact with it. The metal shell is cuboid, which is convenient for processing. The base 3 and end cover 1 of the metal shell should be made of soft magnetic materials with high saturation magnetic flux density, such as iron-cobalt alloy or iron-nickel alloy, so as to prevent the internal magnetic circuit of the sensor from affecting the surrounding devices and prevent the shell from being damaged. The internal sensing part is affected by external electromagnetic interference. The groove 2 and the inside of the end cover 1 jointly form a cavity, and the cavity is provided with:
[0027] The top of the C-shaped magnetic c...
PUM
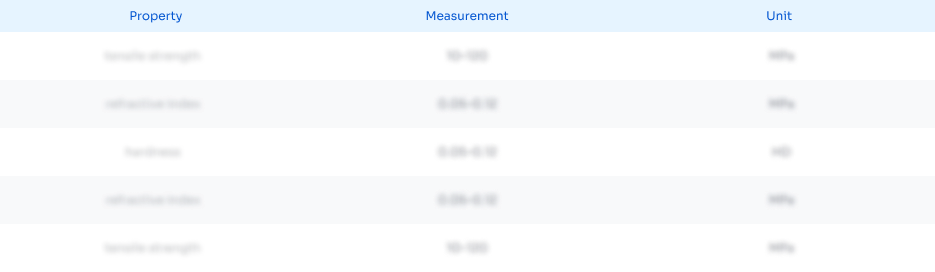
Abstract
Description
Claims
Application Information

- R&D
- Intellectual Property
- Life Sciences
- Materials
- Tech Scout
- Unparalleled Data Quality
- Higher Quality Content
- 60% Fewer Hallucinations
Browse by: Latest US Patents, China's latest patents, Technical Efficacy Thesaurus, Application Domain, Technology Topic, Popular Technical Reports.
© 2025 PatSnap. All rights reserved.Legal|Privacy policy|Modern Slavery Act Transparency Statement|Sitemap|About US| Contact US: help@patsnap.com