A method for removing air bubbles in No. 45 steel
A No. 45 steel and air bubble technology, which is applied to the improvement of process efficiency and the manufacture of converters, etc., can solve the problem of no mention of the removal of steel-slag interface through performance, the number of reusable cycles to be considered, and the lack of refining slag Composition process and other issues to achieve the effect of improving the bubble passing performance, avoiding pore defects, and optimizing the removal effect
- Summary
- Abstract
- Description
- Claims
- Application Information
AI Technical Summary
Problems solved by technology
Method used
Image
Examples
Embodiment 1
[0079] In the present embodiment, the chemical composition of the steel slag formed is: CaO: 50%, Al 2 o 3 : 29%, MgO: 6%, SiO 2 : 9%, CaF 2 : 5%, of which CaO / Al 2 o 3 ≈1.72, Al 2 o 3 / SiO 2 ≈3.2, alkalinity (CaO / SiO 2 )≈5.6, and the rest are unavoidable impurities contained in raw materials.
[0080] In this embodiment, the specific operation process is:
[0081] Oxygen blowing: In the process of converter steelmaking, the top-bottom combined blowing process is adopted to supply oxygen to the metal molten pool to remove excess impurities such as carbon, silicon, phosphorus, etc. in the carbon-saturated molten iron. Oxidation state, to obtain peroxidized molten steel.
[0082] Deoxidation: In this embodiment, a composite deoxidation method combining direct deoxidation and vacuum deoxidation is adopted. Specifically, the peroxidized molten steel is tapped from the converter into the ladle furnace and added to the peroxidized molten steel with a mass ratio of aluminu...
Embodiment 2
[0093] In this implementation, the chemical composition of the steel slag formed is: CaO: 50%, Al 2 o 3 : 28%, MgO: 6%, SiO 2 : 10%, CaF 2 : 5%, of which CaO / Al 2 o 3 ≈1.78, Al 2 o 3 / SiO 2 =2.8, alkalinity (CaO / SiO 2 )=5, and the remaining substances are unavoidable impurities contained in raw materials.
[0094] In this embodiment, the specific operation process is:
[0095] Oxygen blowing: In the process of converter steelmaking, the top-bottom combined blowing process is adopted to supply oxygen to the metal molten pool to remove excess impurities such as carbon, silicon, phosphorus, etc. in the carbon-saturated molten iron. Oxidation state, to obtain peroxidized molten steel.
[0096] Deoxidation: In this embodiment, a composite deoxidation method combining direct deoxidation and vacuum deoxidation is adopted. Specifically, the peroxidized molten steel is tapped from the converter into the ladle furnace and added to the peroxidized molten steel with a mass rati...
Embodiment 3
[0107] In the present embodiment, the chemical composition of the steel slag formed is: CaO: 50%, Al 2 o 3 : 29%, MgO: 5%, SiO 2 : 10%, CaF 2 : 5%, of which CaO / Al 2 o 3 ≈1.72, Al 2 o 3 / SiO 2 =2.9, alkalinity (CaO / SiO 2 )=5, and the remaining substances are unavoidable impurities contained in raw materials.
[0108] The specific operation process is:
[0109] Oxygen blowing: In the process of converter steelmaking, the top-bottom combined blowing process is adopted to supply oxygen to the metal molten pool to remove excess impurities such as carbon, silicon, phosphorus, etc. in the carbon-saturated molten iron. Oxidation state, to obtain peroxidized molten steel.
[0110] Deoxidation: In this embodiment, a composite deoxidation method combining direct deoxidation and vacuum deoxidation is adopted. Specifically, the peroxidized molten steel is tapped from the converter into the ladle furnace and added to the peroxidized molten steel with a mass ratio of aluminum-iro...
PUM
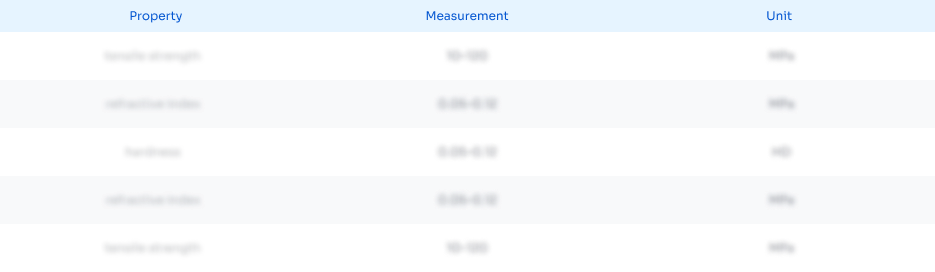
Abstract
Description
Claims
Application Information

- R&D
- Intellectual Property
- Life Sciences
- Materials
- Tech Scout
- Unparalleled Data Quality
- Higher Quality Content
- 60% Fewer Hallucinations
Browse by: Latest US Patents, China's latest patents, Technical Efficacy Thesaurus, Application Domain, Technology Topic, Popular Technical Reports.
© 2025 PatSnap. All rights reserved.Legal|Privacy policy|Modern Slavery Act Transparency Statement|Sitemap|About US| Contact US: help@patsnap.com