Sintering method for reducing solid fuel consumption ratio
A technology of sintering method and fuel consumption ratio, which is applied in the field of sintering to reduce the solid fuel consumption ratio, and can solve problems such as high MgO content of unsintered ore, wear of injection pipes and coal injection guns, and influence of pulverized coal combustion, etc., to achieve reduction Effects of solid fuel consumption, stable combustion, and stable energy supply
- Summary
- Abstract
- Description
- Claims
- Application Information
AI Technical Summary
Problems solved by technology
Method used
Examples
Embodiment Construction
[0017] The invention discloses a sintering method for reducing the solid fuel consumption ratio, comprising the following steps,
[0018] S1. Quantitative addition step, adding a special lower hopper at the position of the raw coal feeding belt, adding heavy magnesium oxide to the raw coal through the special lower hopper, adding heavy magnesia according to 1.0% to 10% of the raw coal feeding amount % join, and enter the raw coal bunker together with the raw coal;
[0019] S2, the mixed pulverized coal preparation process, the raw materials mixed in step S1 are sent to the coal mill to make mixed pulverized coal, wherein the oxygen content at the entrance of the coal mill is ≤ 7%, and the oxygen content at the outlet of the coal mill is ≤ 10%, The inlet temperature of the coal mill is 40-50°C lower than the ignition point of the mixed pulverized coal, and the outlet temperature of the coal mill is 75°C-85°C. The outlet temperature of the powder collector is ≤85°C, the proport...
PUM
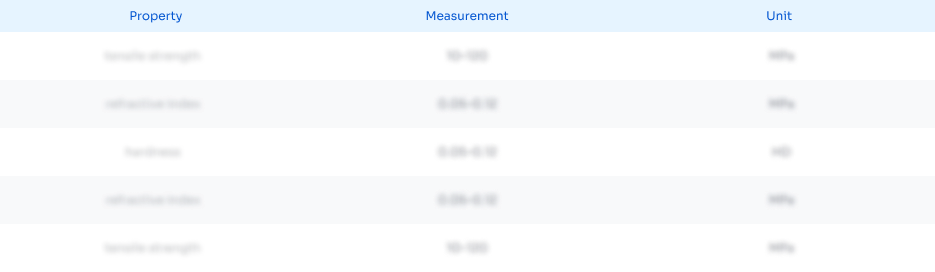
Abstract
Description
Claims
Application Information

- R&D
- Intellectual Property
- Life Sciences
- Materials
- Tech Scout
- Unparalleled Data Quality
- Higher Quality Content
- 60% Fewer Hallucinations
Browse by: Latest US Patents, China's latest patents, Technical Efficacy Thesaurus, Application Domain, Technology Topic, Popular Technical Reports.
© 2025 PatSnap. All rights reserved.Legal|Privacy policy|Modern Slavery Act Transparency Statement|Sitemap|About US| Contact US: help@patsnap.com