Novel heat-resistant PVC profile and preparation method thereof
A technology of PVC resin powder and profiles, which is applied in the field of new heat-resistant PVC profiles and its preparation, can solve problems such as poor heat resistance, and achieve improved heat resistance, little change in impact strength and tensile strength, and excellent overall performance Effect
- Summary
- Abstract
- Description
- Claims
- Application Information
AI Technical Summary
Problems solved by technology
Method used
Examples
Embodiment 1
[0019] 100 parts of PVC resin, 5 parts of heat-resistant modifier, 3.8 parts of stabilizer, calcium carbonate (CaCO 3 ) 18 parts, toughening agent 9 parts, processing modifier 0.5 parts, titanium dioxide 5 parts, lubricant 0.7 parts; mix and discharge the above-mentioned various ingredients; add the dry powder pre-mixed in the above steps into the extruder Profile production; high-speed stirring, when the temperature reaches 110°C, stir for 4 minutes, enter the cold mixer until the material is discharged at 45°C; the temperature setting of each zone of the extruder: the conveying section is 150°C, the compression section is 170°C, the melting section is 180°C, Machine head 175°C.
Embodiment 2
[0021] 100 parts of PVC resin, 10 parts of heat-resistant modifier, 4.3 parts of stabilizer, calcium carbonate (CaCO 3 ) 16 parts, toughening agent 10 parts, processing modifier 0.7 parts, titanium dioxide 6 parts, lubricant 0.8 parts; mix and discharge the above-mentioned various ingredients; add the dry powder pre-mixed in the above steps into the extruder Profile production; high-speed stirring, when the temperature reaches 110°C, stir for 4 minutes, enter the cold mixer until the material is discharged at 45°C; the temperature setting of each zone of the extruder: the conveying section is 150°C, the compression section is 170°C, the melting section is 180°C, Machine head 175°C.
Embodiment 3
[0023] 100 parts of PVC resin, 15 parts of heat-resistant modifier, 4.9 parts of stabilizer, calcium carbonate (CaCO 3 ) 13 parts, toughening agent 10 parts, processing modifier 0.9 parts, titanium dioxide 7 parts, lubricant 0.1.1 parts; mix and discharge the above-mentioned various ingredients; add the dry powder pre-mixed in the above steps to extrude Produce profiles in the machine; stir at high speed, when the temperature reaches 110°C, stir for 4 minutes, enter the cold mixer until the material is discharged at 45°C; the temperature setting of each zone of the extruder: the conveying section is 150°C, the compression section is 170°C, and the melting section is 180°C ℃, head 175 ℃.
PUM
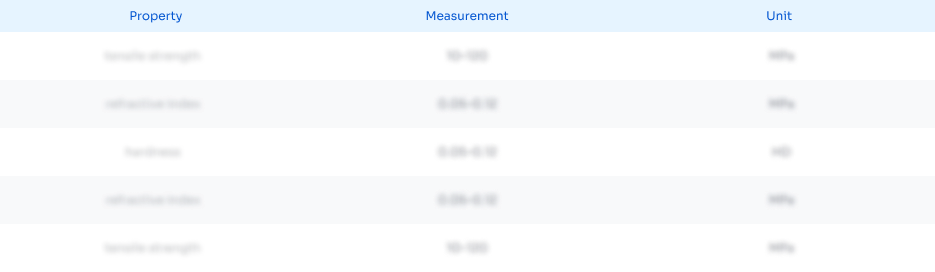
Abstract
Description
Claims
Application Information

- R&D Engineer
- R&D Manager
- IP Professional
- Industry Leading Data Capabilities
- Powerful AI technology
- Patent DNA Extraction
Browse by: Latest US Patents, China's latest patents, Technical Efficacy Thesaurus, Application Domain, Technology Topic, Popular Technical Reports.
© 2024 PatSnap. All rights reserved.Legal|Privacy policy|Modern Slavery Act Transparency Statement|Sitemap|About US| Contact US: help@patsnap.com