A small high-low cycle composite fatigue in-situ testing machine providing orthogonal loading
An in-situ test and fatigue technology, applied in the direction of applying repetitive force/pulsation force to test the strength of materials, can solve the problems of high cost, poor economy, high manufacturing cost, etc., to avoid energy loss, stable loading path, and structural size. small effect
- Summary
- Abstract
- Description
- Claims
- Application Information
AI Technical Summary
Problems solved by technology
Method used
Image
Examples
Embodiment Construction
[0031] The present invention will be further described below in conjunction with the accompanying drawings and embodiments.
[0032] The in-situ testing machine provided by the present invention can carry out the high-low cycle composite in-situ fatigue test of orthogonal loading for the flat plate test piece, and the length direction of the test piece is defined as the axial direction (i.e. the length direction of the testing machine), and the thickness direction of the test piece ( That is, the height direction of the testing machine) is vertical.
[0033] figure 1 , figure 2 The general structure of the invention is given. Among them, the load transmission mechanism 1 and the piezoelectric drive group 2 form a low-cycle drive unit, which provides low-cycle fatigue loads for the test piece 5; the dielectric elastomer 10 is a high-cycle drive unit, which provides high-cycle vibration loads for the test piece 5; Shaft clamp 3, low-circle left clamp 4, low-circumference rig...
PUM
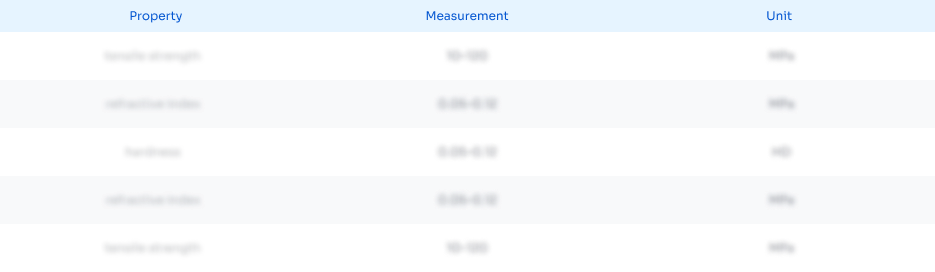
Abstract
Description
Claims
Application Information

- Generate Ideas
- Intellectual Property
- Life Sciences
- Materials
- Tech Scout
- Unparalleled Data Quality
- Higher Quality Content
- 60% Fewer Hallucinations
Browse by: Latest US Patents, China's latest patents, Technical Efficacy Thesaurus, Application Domain, Technology Topic, Popular Technical Reports.
© 2025 PatSnap. All rights reserved.Legal|Privacy policy|Modern Slavery Act Transparency Statement|Sitemap|About US| Contact US: help@patsnap.com