Polishing process for back plate in target material assembly
A process and target material technology, which is applied in the polishing process of the back plate in the target component, can solve the problems affecting the effect of the back plate and the impact of target sputtering, so as to prolong the service life, improve the polishing efficiency, and eliminate the surface The effect of stress
- Summary
- Abstract
- Description
- Claims
- Application Information
AI Technical Summary
Problems solved by technology
Method used
Examples
Embodiment 1
[0028] This embodiment provides a polishing process for the back plate in the target assembly, the polishing process includes sequentially performing first mechanical polishing and second mechanical polishing on the target back plate;
[0029] The abrasive belt used in the first mechanical polishing is a non-woven endless belt of 600#, the rotating speed of the abrasive belt is 11m / min, the feed rate is 9m / min, and the rotating speed of the polishing wheel is 5m / min;
[0030] The abrasive belt used in the second mechanical polishing is a 240# non-woven endless belt, the rotational speed of the abrasive belt is 6m / min, the feed speed is 5m / min, and the rotational speed of the polishing wheel is 9m / min.
[0031] The dirt and surface stress on the surface of the backplane are removed, and the service life is prolonged. It is qualified after polishing for 30 minutes.
Embodiment 2
[0033] This embodiment provides a polishing process for the back plate in the target assembly, the polishing process includes sequentially performing first mechanical polishing and second mechanical polishing on the target back plate;
[0034] The abrasive belt used in the first mechanical polishing is a non-woven endless belt of 600#, the rotating speed of the abrasive belt is 13m / min, the feed rate is 6m / min, and the rotating speed of the polishing wheel is 7m / min;
[0035] The abrasive belt used in the second mechanical polishing is a 240# non-woven endless belt, the rotational speed of the abrasive belt is 5 m / min, the feed speed is 3 m / min, and the rotational speed of the polishing wheel is 10 m / min.
[0036] The dirt and surface stress on the surface of the back plate are removed, and the service life is prolonged. It is qualified after polishing for 25 minutes.
Embodiment 3
[0038] This embodiment provides a polishing process for the back plate in the target assembly, the polishing process includes sequentially performing first mechanical polishing and second mechanical polishing on the target back plate;
[0039] The abrasive belt used in the first mechanical polishing is a non-woven endless belt of 600#, the rotating speed of the abrasive belt is 12m / min, the feed rate is 7m / min, and the rotating speed of the polishing wheel is 6m / min;
[0040] The abrasive belt used in the second mechanical polishing is a 240# non-woven endless belt, the rotational speed of the abrasive belt is 7m / min, the feed speed is 7m / min, and the rotational speed of the polishing wheel is 8m / min.
[0041]The dirt and surface stress on the surface of the backplane are removed, and the service life is prolonged. It is qualified after polishing for 27 minutes.
PUM
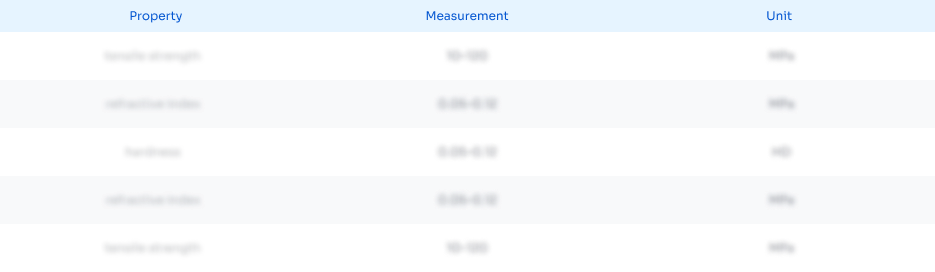
Abstract
Description
Claims
Application Information

- R&D
- Intellectual Property
- Life Sciences
- Materials
- Tech Scout
- Unparalleled Data Quality
- Higher Quality Content
- 60% Fewer Hallucinations
Browse by: Latest US Patents, China's latest patents, Technical Efficacy Thesaurus, Application Domain, Technology Topic, Popular Technical Reports.
© 2025 PatSnap. All rights reserved.Legal|Privacy policy|Modern Slavery Act Transparency Statement|Sitemap|About US| Contact US: help@patsnap.com