Graphite composite sealing gasket processing system
A composite sealing and processing system technology, which is applied in the field of graphite composite sealing gasket processing and processing systems, can solve the problems of poor control of precision, low efficiency, labor consumption, etc., so as to avoid manual feeding , improve efficiency and accuracy, and reduce the effect of human labor
- Summary
- Abstract
- Description
- Claims
- Application Information
AI Technical Summary
Problems solved by technology
Method used
Image
Examples
Embodiment Construction
[0026] The embodiments of the present invention will be described in detail below with reference to the accompanying drawings, but the present invention can be implemented in many different ways defined and covered by the claims.
[0027] Such as Figure 1 to Figure 8 As shown, a graphite composite sealing gasket processing system includes a collection device 1, a cutting device 2, a feeding device 3 and a vertical plate 4, the bottom end of the collection device 1 is fixedly connected to the ground through a support column, and the cutting device 2 comes out The material end is located directly above the corresponding position of one end of the collecting device 1, the cutting device 2 is fixedly installed on one end of the vertical plate 4, the bottom end of the vertical plate 4 is fixedly installed on the ground, and the top end of the cutting device 2 is fixedly installed with a feeding device 3;
[0028] The collection device 1 includes a driving motor 11 fixedly installe...
PUM
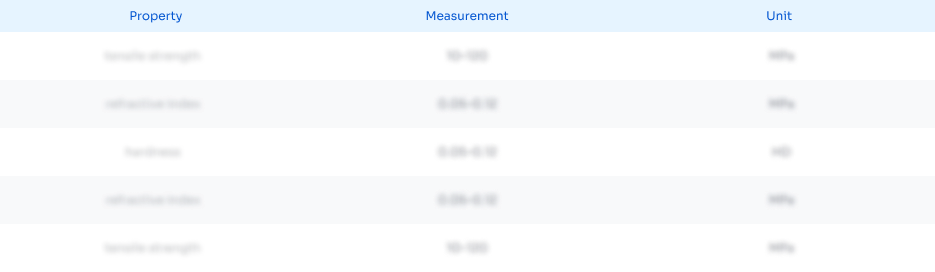
Abstract
Description
Claims
Application Information

- R&D Engineer
- R&D Manager
- IP Professional
- Industry Leading Data Capabilities
- Powerful AI technology
- Patent DNA Extraction
Browse by: Latest US Patents, China's latest patents, Technical Efficacy Thesaurus, Application Domain, Technology Topic, Popular Technical Reports.
© 2024 PatSnap. All rights reserved.Legal|Privacy policy|Modern Slavery Act Transparency Statement|Sitemap|About US| Contact US: help@patsnap.com