Alloyed powder and laser alloying method for corrosion-resistant layer for automobile skin
A technology of laser alloying and corrosion-resistant layer, which is applied in the direction of coating, metal processing equipment, metal material coating technology, etc., can solve the problems that do not meet the requirements of saving and green manufacturing, waste is difficult to deal with, and energy consumption is large. to achieve large-scale production, low maintenance costs, and reduced energy consumption
- Summary
- Abstract
- Description
- Claims
- Application Information
AI Technical Summary
Problems solved by technology
Method used
Image
Examples
Embodiment 1
[0039] This embodiment provides a corrosion-resistant layer alloying powder for automobile skin and a laser alloying method. The latest development of ultra-broadband lasers is used to achieve rapid and efficient alloying preparation on the surface of thin strip steel. It is characterized in that, by weight percentage, the mass percentage composition of the alloyed powder is: C 0.03%, Al 0.2%, Mn 0.35%, Cr 20%, Mo 8%, Nb 4.25%, P ≤ 0.030%, S ≤ 0.030%, Ni balance, the particle size distribution of the alloying powder used: 400~525 mesh; the raw material composition is according to the above alloy ratio Proportioning is carried out, and then the small alloy ingot is vacuum smelted, the small alloy ingot is melted by medium frequency induction heating, and the powder is made by gas atomization method, and then the powder is sieved to obtain the desired alloyed powder, which is prepared by gas atomization method Alloyed powder spherical shape is good. A laser alloying method for ...
Embodiment 2
[0042]This embodiment provides a corrosion-resistant alloying powder for automobile skin and a laser alloying method. The latest development of ultra-broadband lasers is used to achieve rapid and efficient alloying preparation on the surface of thin strip steel plates. In terms of weight percentage, the mass percentage composition of the alloyed powder is: C 0.05%, Al 0.3%, Mn 0.45%, Cr 23%, Mo 10%, Nb 4.25%, P≤0.030%, S≤0.030%, Ni balance, the particle size distribution of the alloyed powder used: 400~525 mesh; the raw material components are proportioned according to the above alloy ratio, and then Carry out vacuum melting of small alloy ingots, apply medium frequency induction heating to melt small alloy ingots, use gas atomization method to make powder, and then carry out particle size sieving on the powder to obtain the required alloyed powder, and the shape of alloyed powder spherical shape prepared by gas atomization method good. A laser alloying method for a corrosion...
Embodiment 3
[0045] This embodiment provides a corrosion-resistant layer alloying powder for automobile skin and a laser alloying method. The latest development of ultra-broadband lasers is used to achieve rapid and efficient alloying preparation on the surface of thin strip steel plates. In terms of weight percentage, the mass percentage composition of the alloyed powder is: C 0.04%, Al 0.2%, Mn 0.45%, Cr23%, Mo 10%, Nb 3.15%, P≤0.030%, S≤0.030%, Ni balance, the particle size distribution of the alloyed powder used: 400~525 mesh; the raw material components are proportioned according to the above alloy ratio, and then carried out Vacuum smelting small alloy ingots, applying medium frequency induction heating to melt small alloy ingots, using gas atomization method to make powder, and then sieving the powder to obtain the desired alloyed powder, the alloyed powder balls prepared by gas atomization method have good shape . A laser alloying method for a corrosion-resistant layer of an autom...
PUM
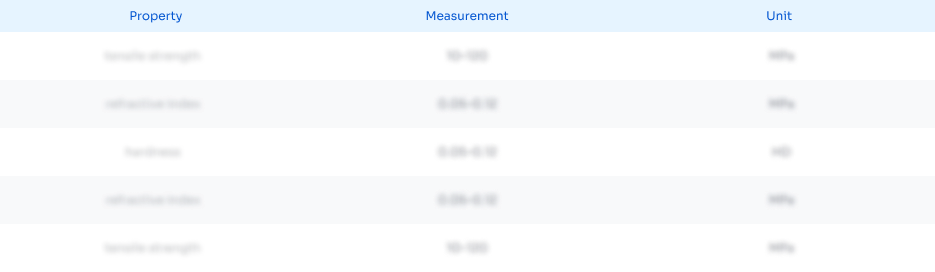
Abstract
Description
Claims
Application Information

- R&D Engineer
- R&D Manager
- IP Professional
- Industry Leading Data Capabilities
- Powerful AI technology
- Patent DNA Extraction
Browse by: Latest US Patents, China's latest patents, Technical Efficacy Thesaurus, Application Domain, Technology Topic, Popular Technical Reports.
© 2024 PatSnap. All rights reserved.Legal|Privacy policy|Modern Slavery Act Transparency Statement|Sitemap|About US| Contact US: help@patsnap.com